|

テクノバ株式会社 |
|
|
 |
|
(財)日本生産性本部 生産性新聞 2012年(平成24年)5月15日 火曜日 |
A現場での異常管理の考え方 日本生産性本部 生産性新聞 2012年5月15日
「異常管理」の確実な遂行には事前の綿密な準備を
異常は正常と異状の間にあり、正常からの変化、即ち異常発生を識別し、これに適切に対処することにより、異状の発生を抑制する事が異常管理であることは前(初)回に述べた。今回は現場における異常管理の考え方について考えてみたい
我が国の職場は極めて厳しい経済環境下にある。その為に企業は、非正規雇用者や外国人労働者の労働力に、頼らざるを得ないのが現実である。結果として職場に経験の浅い者や、コミュニケーションの難しい者が増加する傾向にある。
このような経験不足の労働者が多い職場では、労働者に作業に必要な知識や経験が不足している為、作業の中で発生する事象の変化(異常の発生など)に対して、適切に即応していくことが、かなり困難であるのが実情である。そのため労働者の経験不足を補うためにも、積極的に異常管理を実施して、異状の発生を抑制し、発生するトラブルを未然に防ぐ必要がある。
今まで同質な労働者から形成されていた日本の職場においては、ベテラン労働者が言葉の不自由な労働者や、仕事を熟知していない作業者と、仕事上のコミュニケーションを確実に行うのはかなり難しい。そのため前もって的確なコミュニケーションの方法について、日頃から検討準備を行っておく必要がある。
このような事情は、異常管理の遂行においても考慮しなければならない。そのため例えば外国人労働者に対しては、出来るだけ現地の言葉で表現する、平易な言葉を使用する、現地で現物を見て互いに事実の確認をするなどの配慮をしなければならない。同様に経験や知識の少ない者に対しても、なるべく平易に説明することが必要である。
異常管理を確実に成功させるには、まず事前に異常管理について教育や訓練を行っておかなければならない。第1ステップでは、まず@異常とは何かを異常発生の前に定義しておく、これが曖昧だと労働者は何が異常であるか判断できない、A書き易い異常報告書の書式を作成しておくと、的確な報告をし易くなる。B異常発生に備え対応組織を作り、対応図を作成する。C異常発生時に抜けが生じないように、異常処理規定を定めておく。
第2ステップでは、D異常発生に備え、発生時に慌てないように予行演習をしておく。第3ステップでは、異常の確認を迅速に行う。この時現場・現物・現実を直視することを忘れない(三現主義)。
第4ステップでは直ちに的確な応急処置を行い、影響を最小に留めることに努力する。生産の中止・継続の判断、異常ロット識別、関連部署等への連絡など行わなければならないことは沢山ある。
第5ステップでは再発防止のために、異常処理規定を確実に守る。もしも不備や抜けがあれば、直ちに追加実施をして完全な処置を行う。処理規定や報告書書式に、不備や改善の必要があれば改訂し定着する。
このような異常管理のステップを事前準備することにより、異常状態で発見し、それに適切な対応ができ、異状の発生を抑制することが可能になる。異常管理の確実な遂行のためには、綿密な準備が必要であることを忘れてはならない
|
|
|
(財)日本生産性本部 生産性新聞 2012年(平成24年)4月15日 火曜日 |
@[異常管理」は何故必要か
「異状」と「正常」の間にある、重要な何かが「異常
「異常管理」と聞いても、直ちにピントこない方は多いに違いない。実際、異常管理は一般には余り馴染みのない言葉であろう。初回は異常管理とは何か、また、その必要性について考えてみたい。
工場の生産性向上支援をさせて頂いているので、多くの工場で生産(作業)日報の類を目にする。大方の日報の隅には備考欄があり、そこに毎日のように「異状なし」もしくは「問題なし」と、担当者により記入されている。その上、ご丁寧に責任者の捺印がある。冗談半分でいっその事「異状なし」と印刷しておいたら如何ですかと申し上げる。
連日の「異状なし」の記載にも関わらず、現実にはかなりの異状が発生している。一体何故だろうか、異状はないのに異状が発生しているのである。ここで「異状なし」の異状を試みにトラブル(或は問題)と置き換えたら分り易い。「異状なし」はトラブル(明確な問題)が発生していないだけで、「異状なし」は正常であるとは限らないのである。
実際、発生したトラブルを調べると、大抵は突然には発生していない。「突然に」と思っても後から振り返ると、必ずと言って良いほど予兆の現象が発生している。例えば機械のチェーンが突然切れたと報告があったとする、担当者に訊ねると大抵の場合、「そう言えば、ここ2,3日前から、カタカタ或はキーキーと鳴っていたような気がする」と言うような話を聞くことになる。
作業者にとってチェーンが切れるまでは、例え異音が発生しても作業に支障がないので、チェーンの異音は異状ではないのである。従って日報の記録も「異状なし」になる。仮に異音発生を意識はしていても、大抵の人間(作業者も含めて)は面倒なことは避けたいので、取りあえず作業に支障のない現象をわざわざ問題にしようとは思わないのである。
このように考えると、異状と正常の間に重要な何かがあるような気がする。それを「異常」と考えている。この例で言えば、チェーンが異音を発する前の機械の状態を正常とし、チェーンが切れて機械が停止した状態を異状とすると、その間にあるチェーンが異音を発し始めた時が異常の発生であると考える。
作業者がチェーンの切れる前、即ちチェーンが異音を発し始めた時に「異常」に気付けば、チェーンの切断による機械の停止、即ち生産の停止は防げたはずである。すなわち何時もの正常な状態から、兆候(予兆)の段階で手を打てばトラブルは防げる。チェーンが出す警告音である異音に対処すれば、具体的には例えばチェーンの緩みを取る、或は注油をするなどの対処を行えば、チェーンは切れなかったであろう。或は切れる前に取り替えることも可能であった。
この様に正常な平常の状態を掌握し、そこからの変化に感度を上げて気付き、対処することで異状の発生を抑制することが異常管理である。
|
|
|
(財)日本生産性本部 生産性新聞 2011年(平成23年)11月15日 火曜日 |
前兆管理・前兆管理を現場で実践
観察力・判断力・実行力がトラブルを防ぐ力に
「異常管理」の意義と実践のポイント
「異常管理」という言葉を、初めて目にされた方も多いのではないかと思う。斯く言う筆者も当初その意味を正確に理解していなかった。何故なら例えば(社)日本経営工学会編の生産管理用語辞典にも「異常管理」についての項目はないからだ。「異常管理」とはいわゆるトヨタ用語の一つであり、その意味は前兆管理・予兆管理と捉えた方が理解しやすい。これは例えばがけ崩れが発生する前に、沢の水が濁るとか、小石が転がるとか、大事故が発生する前には、何かしらの前兆が必ずあると考える管理法である。
品質事故の場合も同様の現象が起きる。すなわちこのような前兆を事前に察知して、それに対処出来れば事故や災害を予防する、あるいは避けることが出来ると言う考え方である。
このような考え方を生産現場で実践したものが異常管理である。これはクレームやトラブルの原因になる品質不良の発生前に、製造現場で起きる今までの正常状態と異なる変化(異常)に素早く気付き、適切な対応をとることによってトラブル発生を回避しようとする品質管理法の一つである。
例えば身近な現場での「異常管理」の事例として、機関車やバスの運転手が始業前に小さなハンマーで車輪や動力装置を軽く叩く「始業点検作業」がある。毎日毎日の始業点検で正常時の打音を記憶することにより、もしも装置に亀裂などの異常が生じたとき、打音の違いによって直ちに異常に気付くことができるのである。この気付きに対応することにより大きな事故から免れる事が出来るのである。
しかしながら人は都合の悪いことは判断の対象から外す、不都合なことに対して目をつぶりがちにある。例えば少しいつもと違うなと思っても、まだそれほどでもないだろうとか、今日の作業が終わった後で確かめようとか考えてしまう。
実際そのような場面に製造現場においても遭遇する。作業者が少しおかしいなと感じていても、例えば報告書を書くのが嫌だ、或は面倒くさい、場合によっては上役から小言を言われるのが嫌だなどの理由で放置される例は多い。
このように事実に基づいて客観的に判断し実行ことは案外難しい。従って異常管理の第一歩は正常とはどのような状態であるかを如何に正確に掌握しているか、これに基づき異常を察知した時に直ちに対処できるかに尽きる。正常な状態を正確に掴んでいなければ、その変化(異常)を察知することなど出来ない。
しかし人間の記憶は曖昧で時には思い込みもあり、徐々に起きる微妙な変化に気付くことは案外と難しい。このような人間の陥りやすい判断力の低下に対しては、管理図などのツールの活用は有効である。全ての物は完全に安定していることはまれであり、いつもわずかに状態は変動する。避けることの出来ない揺らぎのような変動と異常原因となる変動を、ツールの使用によって記憶や勘に頼らずに的確に識別することが可能になる。
思い込みや過信によって大災害が発生した今こそ、異常管理は必要とされているのではなかろうか。人の持つ第六感も大きな効果を示すこともあるが、客観的な研ぎ澄まされた観察力、判断力、実行力が大きなトラブルを防ぐ力となる。このような点からますます異常管理は重要になってくるであろう。異常管理に関心をお持ちの方は拙著「よくわかる『異常管理』の本」を参考にしていただきたい。日本の製品・サービスの品質向上、社会の安全に異常管理の考え方が役立つことを期待している。
|
|
|
(財)日本生産性本部 生産性新聞 2011年(平成23年)6月5日 日曜日 |
「食品製造業の生産性向上にむけて」
熱意と努力を持った生産性向上への取り組みが重要に
製造業中従業者数最大の、食品製造業の生産性は、製造業平均の約60%しかない。食品製造業は零細小企業が多い為に、生産効率が低いとされてきた。ところが零細小企業の従業者比率は、製造業平均とほぼ同じで、これを低生産性の原因とするのは誤りである。食品製造業では500人以上の大工場の従業者は極端に少なく、むしろ中規模事業所に集中している。また食品の作業特性が悪いために、生産性は低いと言われる。それなら海外の食品製造業も、生産性は低いはずである。ところが欧州諸国の食品製造業の生産性は、日本の製造業平均と同等か、むしろ高い。無論食品に多少の違いはあるが、多くの加工食品は日本とそれほどの違いはない。
一般に工場規模拡大により生産性は向上する。製造業平均では零細工場と1000人超の大工場の、生産性には約5倍の開きがある、ところが食品製造業は約2倍しかない。規模拡大効果が小さいことは、大工場が少ない原因にもなっている。1000人超の工場の生産性は、同規模対比で製造業平均の約40%しかない。また300人超の工場の生産性は60%に届かない。故に食品製造業の低生産性の原因は大規模工場にある。これは食品製造業の生産管理技術が不足しているためと考えられる。昔から「人は城、人は石垣、人は堀」と言われるように、国(企業)の優劣は城(工場)ではなく、人の能力の差である。
生産性は「労働の質*」と相関があり、食品製造業のそれは製造業中最も低い。平均勤続年数12年に対し、食品製造業は8年しかない。食品製造業は勤続年数が、何故短いのか再考の必要がある。教育訓練は従業者の職務遂行能力を向上するため、高生産性業種は多くの教育訓練費を投資している。その結果、他の製造業では生産性は向上しているにも拘らず、投資の少ない食品製造業は低下している。
経済成長は、資本増加、労働増加、全要素生産性向上によるが、先進国では全要素生産性が主である。全要素生産性は資本と労働を除く全要素を含み,主に技術革新・規模経済性・経営革新・労働能力伸長・生産効率改善などの「広義の技術進歩」とされている。例えば、機械導入で生産性が上昇すれば、資本増加によるものであり、使いこなして生産性が上がれば,全要素生産性向上によるものである。
日本生産性本部の創立50周年で、奥田元日本経団連会長が「常に向上心を忘れずに現場で小さな発明、改良に打ち込む監督者たちや、QCサークルなどの小集団活動で、品質改善やコストダウンに知恵を出し合う現場の人たち、こうした無数の普通の人たちが我が国の企業を支えてきた。」と述べているように、監督者や現場の人々の熱意と努力があってこそ生産性は向上する。
生産性向上への取り組み評価は難しいが、産業別に従業者10万人当たりの、QCサークル登録数を比較した。登録数を生産性向上の熱意と見ると、産業別の熱意と全要素生産性には高い相関がある。全要素生産性の本質は曖昧な「広義の科学技術の発展」より、生産性向上への熱意と努力であると考えている。
短い勤務年数,教育訓練機会等の欠如が、食品製造業の生産性向上を妨げてきた。全要素生産性の本質が、生産性向上の熱意と努力であるならば、食品製造業は熱意と努力を持って、生産性向上に取り組む必要がある。労働の質を高めるためにも、勤続年数延長、生産管理技術の教育訓練を実行していく必要がある。これにより食品製造業は確実に生産性を向上出来るものと信じる。
*労働の質:性別、学歴別、勤続年数別に集計された所定内給与を、産業ごとの労働者構成で加重平均して、単位賃金を求めてこれを指標にしたものである。
|
|
|
食品工業(光琳)Vol.53 No.21 2010年(平成22年)11月15日号 |
「生産性向上ツールDVD」
テクノバ梶i奈良市宝来,弘中泰雅社長)では,このたび食品製造業の生産性向上に役立つツールDVD「食品工場のムダ削減・生産性向上・収益アップ」を新発売した。
食品製造業の生産性は極めて低く,改善の余地は沢山ある。それに気付いいない経営者や管理職者も多い。食品製造業の生産性が低いのは,@分業のやり方が理解されていない,A標準化のやり方がわからない,Bライン生産の仕組みが分らない,など生産技術のノウハウ不足にある。このDVDは,こうした食品製造業の共通の問題点を電機製造業の生産の仕方と比較して分りやすく説明した実践的なノウハウが得られる。
DVDの詳しい内容・購入は http://www.technova.ne.jp/tool.html またはhttp://www.technova.ne.jp/.
|
|
|
(財)日本生産性本部 生産性新聞 2010年(平成22年)2月15日 月曜日 |
「生産管理 雑感」 生産管理技術導入による生産性向上の再認識を
ここ10年余り食品工場の生産性向上に取り組んでいる。食品製造業の生産性は大変低く,製造業全体の平均の約60%しかない。食品製造業の中でも,装置型高生産性の食品工場を除く,労働集約型の加工食品工場の生産性が,食品製造業の低生産性を決定付けている。これらの食品工場と接する中で,食品工場の低生産性の原因に,共通点があるように感じるようになった。
その原因とは生産管理技術の欠如である。生産管理のパラダイムはアダム・スミスの「分業」,フレデリック・テーラーの「標準化」,ヘンリー・フォードの「ライン化」,それ以降のトヨタ生産システムをなどと変化して行ったが,低生産性食品製造業はこの変化に追従できていない。いまだに,多くの食品工場の生産管理は前近代的である。
実際,低生産性の食品工場では一人完結型の作業が多く,分業の効果すら理解できていない工場が多い。標準化については実行されている工場は甚だ少ない。実際に製造条件が詳細に文章化されている工場は殆ど無い。したがって作業者に聞くと,各人の作業条件が異なることは日常的で,作業の標準化が,いかに生産性の向上に有効なものであるか理解されていない。ライン化については,設備メーカーによる装置が導入化されており,水練り工場,パン工場などでは,立派なラインが設置されている例も多い。しかし問題は,これらの装置が生産管理的に,有効に活用されているかどうかである。例えばりっぱなコンベアーが設置してあっても,断続的な運転になっている例が多く,ラインバランス,ボトルネック,タクトタイムのような概念を理解している工場は少ない。実際,これらの工場に生産管理手法を導入すると,生産性はかなり向上することを経験している。
このように生産管理手法の導入が,このような食品工場には必要であると痛感している。反面,生産管理系の経営工学科が,その役目が終わったかのように,最近急速に廃止されている。その原因はおそらく受験生の人気が無い,即ち学生が集まらないと言う事であろう。受験生から見れば,良く分らない,就職が良くない,上位校に経営工学科がある大学が少なく,選択対象から外れるなどの理由が考えられる。
このような理由の他に,経営工学系の研究の多くが,例えばトヨタ生産システムなどの研究,あえて言えば事例研究に傾きすぎて,学界が産業界に追従する形になってしまったこと,コンピュータによる課題解法など,実際の現場から離れてしまったことも考えられる。研究が企業の後追い,あるいは実際の現場で余り役に立たなければ,授業料を払ってまで,大学で学ぶ必要があるのかと考えるのは当然であろう。
しかし,現実として食品製造業のように,生産管理技術の導入が遅れている産業もある。また全就業者の43%を超えるサービス産業の低生産性も,国家的問題として前政権では取り上げられた。勿論現在でもその状況は変わっていない。これらはいずれも今まで生産管理学が,あまり対象として取り扱っていなかった領域である。
長い間,絶版だったテイラーの「科学的管理法」が最近復刊された。この機会に生産管理について再考することも良いだろう。自動車産業や電機産業のみが,生産管理学にとっての対象ではないはずである。未だに日本の生産性は高いとは言い難い,いまだに生産性の低い産業が存在していること,また生産管理技術導入により,その生産性が向上することを再認識して,食品製造業を始めとする日本の低生産性産業の生産性を向上させたいものだ。
|
|
|
ベーカーズタイムス 2009年(平成21年)11月10日 火曜日 |
スクラムソフトウェアとテクノバが業務提携
食品工場の生産性向上に力を発揮する生産管理ソフト「アドリブ」を開発・販売しているテクノバ梶i弘中泰雅社長)と、コンピュータシステムの設計・開発・製造・販売を手がける潟Xクラムソフトウェア(大阪市中央区、山本剛社長)が、両社の強みを活かして相乗効果を計り、食品業界に向けて生産管理ソフト「アドリブ」の拡販を図る目的で業務提携した。
生産管理ソフト「アドリブ」は、@生産工程が複雑で工場の全体、細部の掌握が難しく効率的な工場経営が難しい A製品の数が多く、納期が複雑で生産スケジュールが立てられず効率が悪い B現在使用中の基幹システム(ERPなど)の工場管理の機能がなく不便である C工場の効率を上げ、利益がだせるシステムが欲しい D単なる生産順のスケジュールだけでなく設備、労働力などを含む総合的な計画を立てたい E製品あたりの材料費、人件費など製造原価・原価計算をリアルタイムで知りたい、等の食品工場の問題点を解決するソフトで、既にパン業界の中堅企業数社で採用されている。
但し、これまではテクノバ鰍フ弘中社長一人で導入からメンテナンスまでを見ていたため、充分に手が回らない場面もあった。しかし今回の業務提携により、コンピュータのハード・ソフトに精通したスタッフ陣がフォローに当たれるため、今後は、テクノバ鰍ヘコンサルタント業務、潟Xクラムソフトウェアがカスタマイズ業務を行い、充実した導入体制が組めるようになる。
政権が代わり、最低賃金の引き上げ論議が起こる等、益々厳しさを増す食品業界のために、少しでもお役に立てればと、両社長は話している。
|
|
|
(財)日本生産性本部 生産性新聞 2009年(平成21年)5月15日(金) |
一言 食品製造業の生産性向上は喫緊の課題
食品製造業の生産性を向上できないか考えている。食品系の大学を出て食品企業に勤めたが,縁あって電機メーカーに転職した。
組立産業である電機製造業は大掛かりな装置もなく,当初,生産に興味はなかったが,生産管理システムの素晴らしさに気付き,食品製造業の生産性向上を考えるようになった。
食品製造業の生産性は製造業平均の約6割と極めて低い。製粉や製油等素材型など一部の食品製造業の生産性は製造業平均と比べて遜色ないが,豆腐・蒲鉾(かまぼこ)・パンなどの加工型製造業の生産性は低く,労働集約的で大規模工場であっても,生産性は高くない。
食品製造業は製造業中最大で,製造業の全就労者の13%が勤めている。従って食品製造業の生産性を製造業平均まで上げれば,全製造業の生産性は5%以上改善することが出来る。
殆(ほとん)どの加工型食品工場において生産管理が不足している。生産管理部署のある工場もあるが,実際には受注業務程度のことしかやっていない。食品製造業には農学系の出身者が多いが,多くの農学系大学教員は生産への関心が低く,研究者教育を志向している。
まして生産管理やITの授業のある大学は工学系に比べ少ない。多数の卒業生が食品製造業に就職しているが,優秀な学生の多くは素材型のメーカーに就職しているようだ。人材(無形資産)不足に食品製造業の生産性が低い原因の一つがある様な気がする。
米国の生産性に比較して60%しかないと言われる日本だが,そのまた60%の食品製造業の生産性の低さが一因でもある。食品製造業の生産性を向上させねばならない。
|
|
|
ベーカーズタイムス 2009年(平成21年)4月10日 金曜日 |
テクノバ轄O中泰雅氏の指導を受け
パン工場の生産性向上を図る 潟Wャパン・シーフーズ
潟Wャパン・シーフーズがパン工場の生産性への取り組みを始めた。同社は平成16年に,潟rスタフーズ,潟Wャパン・シーフーズおよび九州近鉄商事鰍フ3社が合併し,商号を潟Wャパン・シーフーズに変更した会社で,パン関連ではコクラン・エネのブランドで,近鉄百貨店内に店舗を構える他,近鉄系の売店や量販店に卸している。
今回の取り組みについて美原センター部長の松村啓伸氏は次のように話す。「弊社は近鉄百貨店の100%子会社で,販売に関してはある程度のノウハウを持っていますが,製造部門に関してはまだまだ弱いところがありました。それで一度,外部の方に専門的に見てもらおうと考えていたところに,ウェブでテクノバの弘中氏のことを知り,これを機会に全社を挙げて生産性に取り組むことに決めました。
とりあえず半年間の契約でお願いし,現在5ヶ月目に入っています。これまでシフトを変えたり様々な取り組みを行い,社員の意識が変わってきたことは感じていましたが,なかなか数字には表れませんでした。しかし,ようやく10日ぐらい前から,少し結果が出るようになってきました。生産性向上に取り組む前は,所定外の労働時間が多い日は25〜30時間もあったが,現在はそれが半分になり,10時間を切る日も出てきたという。
しかし,松村氏はまだまだ目標達成にはほど遠いと話す。「生産性を上げて労働時間を圧縮することだけが最終目的ではありません。圧縮した時間を他の仕事に宛てて,次のビジネスに繋げ,売上拡大を図っていかなければ意味がありません。同じ働くのなら効率よく仕事をすることで売上を拡大し,従業員の人達にもより多くの給料を払えるようにしたい。それが最終目標です。その為には,今まで18時までかかっていた仕事を,掃除まで含めて14時半で終了するようにしなければなりません。そして自己管理の中で継続していくようにする必要があります。
テクノバ轄O中泰雅氏の指導のもとに開かれる定例会議は,ガントチャートを広げ,各部署のチーム長同士で,今より更に改善できる箇所を潰していくための活発な意見交換が行われている。製造現場のチーム長からはこんな声が聞かれた。「今までは自分のポジションだけに集中していて,全体の流れが見えていなかったと感じています。目に見えるチャートを使って意見を交換することで,他の工程がどうなっているのかよくわかりますし,自分の後の工程で頑張っている人達のことを考えながら作業をするようになりました。
|
|
|
生産性新聞 2008年(平成20年)8月25日 (財)経済社会生産性本部 |
食品製造業の全要素生産性向上
”無形資産”の一層の充実を
最近の食に関する話題は食品偽装や食料品に値上げであるが、他にも、特に食品製造に関して根深い問題がある。しかし専門家の間でもこの問題に関心を持つものは余り多くない。その問題とは食品製造業の生産性の低さである。
工業統計表【概要版】(平成18年)をみると、食品製造業は事業所数で全製造業の12.5%、従業員数で13.3%に及ぶ大きなセクターである。にもかかわらず付加価値額は8%しかなく、付加価値額/人は全製造業平均の59.9%しかない。国際競争力のある自動車製造業との比較では1/5以下、テレビなどの情報機器との比較では、1/2以下で、その格差は歴然としている。
工業統計表にある食料品製造業40種のうち、ぶどう糖、砂糖、植物油脂、食用油脂加工、小麦粉、デンプンなど12業種(高生産性業種)の生産性を調べると、高生産性業種の平均付加価値額は1800.9万円/人となり、全製造業平均1308.1万円/人をはるかに上回っている。これらの工場は、概して大企業の省力化された設備整備率の高い装置型のコモディティ食品製造業である。
ところがこれら高生産性業種を除く食品製造業、肉製品、水産、練製品、冷凍水産製品、野菜漬物、パン、生菓子、麺類、豆腐・油揚、冷凍調理食品、惣菜などの製造業(低生産性業種)の生産性は673.4万円/人となり、全製造業の51.5%しかない。したがって食品製造業の生産性向上を考える時は、中小企業の労働集約型工場が多い、この低生産性業種こそが鍵となる。
何故、低生産性業種の生産性は低迷してきたのであろうか。@最近まで、日本の人口は増加しマーケットが拡大した。食品の特性や食糧管理法などにより、国際競争が他業種に比べて少なかったことにより、結果として他産業と比較し努力が少なかった。A機械製造業などと比べ、食品製造業は系列化が少ないため、大企業から生産ノウハウが入らなかった。B歴史のある産業で、経験と勘の職人的体質が残っている。C農学領域のため、経営工学的な手法が入りづらかった。等の理由が考えられる。
谷口(2005)によると、食品製造業は経済成長の一要素である技術進歩による経済成長「広義の技術進歩」を表す、全要素生産性(TFP)が長期にわたり負の値を示している。しかし国際競争力がある自動車(輸送機械)、電気機械などは、逆にいずれも高い正の値を示している。
国際化や活発な研究開発などを行なった企業のTFPは上昇し、生産性を改善している。内閣府調査(2004)によると、食品製造業の研究開発集約度は、確かに製造業中で最も低い業種の一つである。食品製造業の研究開発投資の低さは、TFPの上昇を妨げたと言えるであろう。
IT技術の発展が生産性向上に影響することは広く認められている。一般的に食品製造業のITリテラシーレベルは、他の製造業に比べて低いと感じる。ITリテラシーを含むインタンジブルアセット(Brynjolfsson 2003)の不足が、生産性の向上を妨げているのではないだろうか。これを裏付ける興味深いデータがある。食品製造業の学問的領域は、他の殆どの製造業が工学であるのと異なり、農学領域である。この領域から多く出身者が食品製造業に就職している。農学領域の研究者は他領域に関心が高く、複合的な領域で研究をしているが、その反面情報科学との接点は極めて低い。工学領域では、情報科学を第二専門にしている研究者は1.9%、理学領域では1.3%であるが、農学領域では0.1%で、自然系の中では極めて低く、人文科学系に比較しても低い(西沢ら 2001)。データが少し古いことと、農学系と食品系が必ず一致するわけではないので、断言することは難しいが、現在でもこのような傾向があるとすれば、そこから供給される学生のITリテラシーは概して高くない可能性はある。
|
|
|
トーヨー新報 2008(平成20年)7月21日(月曜日) 発行 |
生産性向上をめざすコンサルティング
テクノバ
食品工場の生産性向上に向けたコンサルティングを行なうテクノバの社長、弘中泰雅さんは、「原材料価格の高騰を嘆いても、経営状態は改善しない。ほんの少しやり方を変えるだけで生産性は驚くほど向上する」と力説する。同社のコンサルティングは、まず各工程の作業状態、作業員の動き、チームとしての作業など実態を調査。そして整理、整頓、清掃などの「根本改善」をはじめ、「作業改善」「職場間協調」「品質保証」「好調保全」「納期短縮」「在庫圧縮」「コスト圧縮」「食品衛生」に至るまでの工場のトータルな状態を診断・評価する。簡単なインタビューと写真撮影のみだから、日常業務の妨げになる心配はない。結果は後日、報告書にまとめて送付されるが、オプションでプレゼンテーションをしてもらうことも可能。
診断期間は1日から長期まで請け負う。一日診断で価格は10万円。診断中もその都度、適切なアドバイスを行なう。「無駄を省けば従業員の疲れが軽減されて生産効率が高まり、人件費削減につながる」と弘中さん。以前診断した製パン工場では、従来の生産スケジュールを組み替え、1ヶ月あたりの残業代を前月比で約百万円も削減することに成功した。これまでに豆腐、納豆、こんにゃくの製造工場も手がけており、作業ロスの原因究明と改善に貢献してきた。
弘中さんは以前、食品工場に勤務していた経験から、食品工場の生産性を妨げる要因として「従来のやり方が最適だと思い込んでいること」を挙げる。「食品工場の製造ラインでは特別な技術が必要とされないため、従業員は最初に教えられた作業をこなすだけで、改善の必要を感じない。外部からの客観的な目で指摘すると、従業員は耳を傾ける場合が多い。とにかく変わらなければ何も改善しない」と訴えている。
|
|
|
|
|
日本食糧新聞 2008年(平成20年)5月14日(水曜日) |
「日本生産管理学会記念講演」テクノバ 弘中泰雅社長語る
業界団体など協力必要 国内食品製造業、生産性向上を
「現在より多くの加工食品が国内で生産されるようになれば、国内総生産(GDP)増加や新たな雇用の創設など多くの効果が生まれてくるのは確実だろう」と語るのは、テクノバ社長の弘中泰雅氏。4月26日に大阪市北区の大阪工大大阪センターで開催された「日本生産管理学会関西支部総会記念講演会」の中で語られたもの。
(社)食品需給研究センターの「食品産業動態調査報告書」によると、05年の加工食品(総合)輸入額は1兆4000億円にも達する。この要因については、氏はわが国の食品製造業における生産性の低さをあげ「生産性が低いために価格競争力もおとり、それが輸入加工食品の増加につながっている」と指摘する。
さらに氏は食品製造業の生産性が向上しない理由として@中小企業が多いA古い職人体質と商慣行が残っているB機械・IT化などの導入が困難−などあげたうえで、「今後、これらを克服して生産性を向上させるには、新技術を使いこなせる人材の教育や技術導入に取り組める企業体質づくり、教育機関からの食品製造業に必要な人材の供給、生産性向上に有効な研究・技術開発の促進−などが重要となってくるだろう。しかし、そのためには自らの努力だけではなく、業界団体や研究・教育機関の積極的な協力も必要になってくるだろう」と指摘した。
「国内生産化は、ひいては食品機械技術や食品研究の発展を促すなど、食品業界全体にも波及効果をもたらすことになる」としたうえで、「そのためには官民が一体となって取り組んでいくことが一番重要だろう」と強調する同氏は、食の安全と国内食品業界の発展を真摯に願う一人である。 (木下猛統)
|
|
|
食品工場長 5月号 2008年 5月1日発行 |
目指せ!生産性向上 E
スケジューリング
生産計画を実行に移すときに、最も注意を払わねばならないのは日程管理である。生産にかかわる機能別の分業を日程計画によって統合するが、この日程管理を行なうのがスケジューリングである。
・・・・・・・・・・・・・・・・・・・・・・・・・・・・・・・
スケジューリングにはいろいろな方法・考え方があるが、生産の最適な組合せを計画し、生産性の向上につなげなければならない。
|
|
|
食品工場長 4月号 2008年 4月1日発行 |
目指せ!生産性向上 D
生産計画・管理の方法
売れる速度に同期して、供給しうる製販サイクルができれば理想である。しかし市場の変化により商品の種類や量は常に変化し、工場の生産力にも制限があるので、製販の速度を同期するのは難しい。
・・・・・・・・・・・・・・・・・・・・・・・・・・・・・・・
このような「生産計画」「生産手配」「進捗管理」を、生産管理のマネジメントサイクルと呼ぶ。このマネジメントサイクルを回すことで生産性を向上しなければならない。
|
|
|
食品工場長 3月号 2008年 3月1日発行 |
目指せ!生産性向上 C
トヨタ生産方式 〜かんばん方式とアンドン方式
今号はトヨタ生産方式(TPS)について述べる。その名前はあまりにも有名だが、食品産業のみならず、その本質に理解されているとは言いがたい。
・・・・・・・・・・・・・・・・・・・・・・・・・・・・・・・
このように、常に異常の改善は行なわれるべきものである。たとえ新しい異常が出なくなっても、何もしなければ緩んで元へ戻ってしまうこともあり、それを直すことも新しい改善と同じ評価を受けるので、改善に限りはない。異常の顕在化は、宝の山と言ってもよい。
|
|
|
食品と開発 2月号 2008年 2月1日発行 |
製パン業界中心に納入実績を持つ生産管理ソフト「アドリブ」
テクノバ(090-8233−3225)は、「工場見える化」、「プロセスの見える化」を実現した生産管理ソフト「アドリブ」を販売し、製パン、冷凍食品、製菓、飲料などで導入され、好評を得ている。
アドリブはラインの稼働状況、作業量、供給労働量、原材料使用量、製品や原材料の在庫など生産に関わる情報を把握することができるため、工程計画の立案が難しいとされる多品種プロセスの生産管理を最適化し、合理的な生産計画(Production
Plan)を容易に立てることができる。現場の端末と生産管理本部をLANで結び全工場の見える化も可能だ。
アドリブの大きな特徴は、ロット/バッチを基点とするプロセス生産フローショップスケジューリングを可能にした点にある。製品の生産条件に基づき、製品ごとの生産数を入力すると、生産スケジュールが表示され、スケジュールはグラフによって工場の見える化がなされるため、生産スケジュールの問題点が一目瞭然でわかる。グラフを見ながら生産順や設備の選択を行なうことにより、生産性を容易に向上できる。またアイテム毎に長期生産計画に見込まれる受注や確定受注などをいれて週ごとの生産数量を設定でき、前年の実績から翌年の前年対比長期計画を自動的に立てられるように工夫されている。生産や在庫の状況もグラフに表示されるので、生産、在庫状況を眼で感覚的に確かめることができる。さらに、当日の必要労働量、供給労働量も表示されるため、無駄のない労働力の割り振りや生産順の変更により必要労働量と供給号動力のバランスを取ることができる。アドリブは、これまで生産計画が難しかった多品目生産のスケジューリングを可能にしただけでなく、その実行の結果も検証でき、工場ごとの最適なアドリブをオーダーメイドで作ることもできる。
導入効果としては、@ラインの各工程のあるべき姿を把握できる。A生産リソースを再現に生かすスケジュールを作成できる。B工場の状況が即座に数値化されて、計数で目標管理ができる ― などが挙げられ、導入企業からは、低コストで無理なく導入でき、在庫の適正化や労働力の効率化により導入コストを確実に回収できるシステムとして高い評価を得ている。
|
|
|
食品工場長 2月号 2008年 2月1日発行 |
目指せ!生産性向上 B
生産管理のパラダイムシフト
今回は食品産業を離れて、生産管理の歴史について解説する。
・・・・・・・・・・・・・・・・・・・・・・・・・・・・・・・
生産管理手法はこのように発展してきた。我々はなぜ歴史を学ばねばならないのだろうか。食品工場の実態が上記いずれのパラダイムの段階に有るのだろうか、冷静に考えてみる必要があろう。
|
|
|
食品工場長 1月号 2008年 1月1日発行 |
目指せ!生産性向上 A
労働生産性向上が必須な労働集約型工場
・・・・・・・・・・・・・・・・・
従来、日本人は勤勉で、日本の生産性は国際的に高いとされてきたが、実際には米国の3分の2しかなく、先進国の中では決して高くない。
産業別の製造原価構成率を示したが、食品製造業の労務費は日本の製造業の平均よりも低い。しかし、パン製造業や和洋菓子のような労働集約型の直接労務費比率は、ほかの産業をはるかに超えて極めて高い。従って、食品工場の生産性を考える場合、装置産業である製粉工場や油脂など「素材型工場」と、「労働集約型工場」の生産性は分けて考えなければならない。
・・・・・・・・・・・・・・・・・
|
|
|
食品工場長 12月号 2007年 12月1日発行 |
目指せ!生産性向上 新連載
生産性がいかに食品企業の経営を左右するか
生産性を上げようとするが、なぜか思いどおりに行かない―。そんな食品工場が多いのではないか。生産性を上げるには手段が必要であり、上がらないことには理由がある。食品工場の場合、その最大の理由は「変化を嫌うこと」だと思う。人心の変化なくして改革・改善はない。本連載をきっかけに、生産性向上を目指す工場が増えることを期待する。
・・・・・・・・・・・・・・
|
|
|
食品機械装置 9月号 2007年 9月1日発行 |
トレーサビリティ時代におけるMES・APS生産管理システム
BSE問題や食の虚偽表示問題等に起因して、「食」に関する様々な課題が顕在化している。消費者の求める情報の提供やリスク管理対象の取り組みのひとつとして、トレーサビリティシステムが注目されている。食品のトレーサビリティとは「生産、処理・加工、流通・販売等のフードチェーンの段階で、食品と食品に関する情報を追跡し、遡及できること」が現段階での概念である。しかしトレーサビリティシステムはあくまで食品の追及、遡及のための仕組みであり、製造工程で衛生管理を直接行なうものではない。したがって安全に対して管理が甘い状態で作ったものを後でトレースするより、製造段階で製品として求められる製造条件をきちっと守って安全な食品を製造することがより大切である。
・・・・・・・・・・・・・
|
|
|
食品工場長 8月号 2007年 8月1日発行 |
FOOMA JAPAN 2007国際食品工業展 誌上レポート
テクノバ 「工場の見える化」で最適の生産管理実現
テクノバ鰍ェ出展して注目を集めたのが、生産管理ソフト「Ad Libitum(アドリブ)」。「工場の見える化を図り、最適化された生産管理を行なうのが特長のソフトだ。
中でも、自慢の機能が「作業の平準化」。その日の生産品目と納期を入力すれば、時間ごとにどのラインでどれだけの労働力が必要かが画面表示されるのだ。これで生産工程や人員配置を変更すれば、合理的なスケジュールを組むことが出来る。
もともと粉物を対象に開発したソフトだけに、製粉・製パン業界を中心に普及が進んでいるが、広範な食品工場で使用できる。会期中はCSV向け弁当・惣菜メーカーを中心に、日配品メーカー担当者が多くブースを訪れた。
|
|
|
食品と開発 8月号 2007年 8月1日発行 |
製パン業界中心に納入実績を持つ生産管理ソフト「アドリブ」
テクノバ(06-6630-7812)は、「工場見える化」、「プロセスの見える化」を実現した生産管理ソフト「アドリブ」を販売し、製パン、冷凍食品、製菓、飲料などで導入され、好評を得ている。
アドリブはラインの稼働状況、作業量、供給労働量、原材料使用量、製品や原材料の在庫など生産に関わる情報を把握することができるため、工程計画の立案が難しいとされる多品種プロセスの生産管理を最適化し、合理的な生産計画(Production
Plan)を容易に立てることができる。現場の端末と生産管理本部をLANで結び全工場の見える化も可能だ。
アドリブの大きな特徴は、ロット/バッチを基点とするプロセス生産フローショップスケジューリングを可能にした点にある。製品の生産条件に基づき、製品ごとの生産数を入力すると、生産スケジュールが表示され、スケジュールはグラフによって工場の見える化がなされるため、生産スケジュールの問題点が一目瞭然でわかる。グラフを見ながら生産順や設備の選択を行なうことにより、生産性を容易に向上できる。またアイテム毎に長期生産計画に見込まれる受注や確定受注などをいれて週ごとの生産数量を設定でき、前年の実績から翌年の前年対比長期計画を自動的に立てられるように工夫されている。生産や在庫の状況もグラフに表示されるので、生産、在庫状況を眼で感覚的に確かめることができる。さらに、当日の必要労働量、供給労働量も表示されるため、無駄のない労働力の割り振りや生産順の変更により必要労働量と供給号動力のバランスを取ることができる。アドリブは、これまで生産計画が難しかった多品目生産のスケジューリングを可能にしただけでなく、その実行の結果も検証でき、工場ごとの最適なアドリブをオーダーメイドで作ることもできる。
導入効果としては、@ラインの各工程のあるべき姿を把握できる。A生産リソースを再現に生かすスケジュールを作成できる。B工場の状況が即座に数値化されて、計数で目標管理ができる ― などが挙げられ、導入企業からは、低コストで無理なく導入でき、在庫の適正化や労働力の効率化により導入コストを確実に回収できるシステムとして高い評価を得ている。
|
|
|
パンニュース 2007年(平成19年)7月25日(水曜日) |
労働環境改善を目指して
「IT化によるベーカリーの売上・利益向上」
(社)日本パン技術研究所は、6月27日、同研究所で6月講演会を開催、テクノバの弘中泰雅氏を講師に招き「IT化によるベーカリーの売上・利益向上」というテーマで講演を行なった。労働環境の改善がベーカリーに求められている昨今、作業効率を上げる必要が出てきている。IT化もそうするための選択肢の一つだ。講演会の内容を抜粋して掲載する。
最初に、パン産業の現状を見てみる。食品産業は事業所数で全体の10.3%、従業員数で全体の13.28%、出荷額で全体の7.64%である。これを平たく言うと日本の全従業員数が10万人いるとすると、食品産業の従業員は1万3280人いるが、出荷額は7640人分しかないということになる。
従業員一人当たり付加価値金額は全産業平均が1237万円、食品産業は757万円、パン産業は727万円となっている。食品産業の生産性は製造業の平均の60%程度しかない。おまけにこの20年間はほとんど生産性が向上していない。それでは、なぜ生産性が低いのであろうか。原因の一つは「IT経営の導入が遅れているから」と見られている。
一昔前のIT化は省力化のための投資であった。しかし、現在のIT化はビジネスの仕組みさえも根本的に変えてしまう威力を持った強力なビジネスツールに変身している。ITの活用が企業が生き残っていくための経営課題に密接に関係し始めた。
最近、企業には3つの変化が起きている。1つ目が業界内での通常の変化、2つ目が社会環境・国際環境の変化、そして3つ目がIT業界が絡んでの変化である。IT業界の変化がほかの業界まで影響を及ぼす、このことを見落としてないだろうか。
ここで企業のIT成熟度について見てみよう。IT成熟度は「IT人材育成度×IT企業文化成熟度×ITインフラ成熟度×IT活用成熟度」で表すことができる。平均的中小企業の到達目標「成熟レベル3」は、次のような状態を言う。
IT人材については、従業員のほぼ全員がパソコンを使うことができる。基幹業務ソフトの要件定義ができる人材はいるが、ITを戦力的に利用できる人の育成はこれから。IT企業文化については、仕事の手順は文書化、標準化されている(ISO9000)。主要業務プロセスは電子データ化されフィードバックや学習が組織的に行なわれている。
ITインフラについては、パソコンはハード、OS,ソフトとも1元管理されている事業所内のパソコンはクライアントサーバーネットワークで接続され、データベースは共有されている。IT活用については、会社としてIT活用の重要度が認識されており、社外との接触のある全従業員に会社のメールアドレスを与え有効に活用している。
ところで、ベーカリーは儲からない、もっと利益を上げたいという声をよく聞く。ベーカリーの現状の問題点はどんなところにあるのだろうか。それは、材料コストがかかりすぎること、商品別の材料原価が正確にわからないこと、労務コストがかかりすぎること、残業が多すぎること、サービス残業の問題、パート・アルバイトが多くシフト作成が煩雑であること、管理が不十分で、実態や問題が把握されていないこと、日報などの報告がない、実情がわからないこと、売上が目標を達成しない事がある。
それらを一気に解決するのが当社ソフト「@店舗」と「アドリブ」である。「@店舗」は、リテールベーカリー繁盛ソフトであり、「仕事の見える化」を図り儲かる生産管理を行なうことができる。具体的には、これを使うことにより、店舗のあるべき姿を把握でき、生産リソースを最大限に生かすスケジュールを作成、ベーカリー状況が即座に数値化されて計数で目標管理できる。生産管理、工程管理、原材料管理、製品管理、勤務シフト作成、仕事量と労働量の適正化、シュミレーション、仕込み計算、経営指標、トレサビリティ支援機能が行なえる。
導入対象は、ミキサー2台以内、オーブン2台以内、ドーナッツフライヤー、リバースシーター1台以内装備のリテイルベーカリー。ソフトウェアの価格は60万円(税別)となっている。
「アドリブ」は経験と勘から科学的な生産にできる食品工場用の生産管理ソフト。複雑な「工場の見える化」を図り、最適化された生産管理を行なうことができる。「@店舗」と「アドリブ」の違いは、「アドリブ」は量産工場用ソフトで各工場の仕様に合わせ、テーラーメイドで作るソフトで数百万円以上になる。量産工場の生産状況は工場ごとに異なるため、実態に合わせて工場ごとに作成する。しかし高額なため、小規模のリテールベーカリーには導入が難しい面があった。「@店舗」は価格にかかわらず、非常に高い性能を持っている。
「@店舗」はリテイルベーカリー用のパッケージソフトでプログラムのカスタマイズはできない。しかし、ベーカリーの条件を入力することで実用上のカスタマイズができるため、ほとんどのリテールベーカリーで使用でき、専用のオペレータは必要ない。当社は、今後もベーカリーや製パン工場を始めとする食品産業の生産性の向上のために貢献したいと考えている。
|
|
|
ベーカーズタイムス 2007年(平成19年)6月10日 日曜日 |
福山市のピーターパンがリテール向け『@店舗』を導入
生産性2割アップを目指す
広島県福山市の中学校や高校の売店でパンを販売する潟sーターパン(本社=広島県福山市、広川徹社長)が、テクノバ梶i本社=大阪市、弘中泰雅社長)が開発したリテイルベーカリー繁盛シフト『@店舗』を導入。生産性の向上に取り組んでいる。「昔から計画を立てて生産しないとダメだということで、縦横の表を作って毎日の発注書を書いていましたが、本当に大変で間違いも起こる。それでベーシックのコンピュータに置き換えて、自前で作ったモノを使っていました」
広川社長がテクノバ鰍フソフトを初めて知ったのは数回前のモバック。同社がブースを出し、セミナーも行っていた。「興味があり、何度か見せてもらいましたが、大変そうだし、高そうだということで、通り過ぎていたんです」ところが、今年2月のモバックで紹介されたリテイルベーカリー繁盛シフト『@店舗』は、中小でも使えるように内容を絞り込み、価格も60万円+税の設定。しかも今ならモバックキャンペーンとして半額で導入できることを知った。「本当はその日に帰る予定にしていたんですが、日程を一日延ばして小間に立ち寄り、弘中社長にお話を伺うことにしたんです」話を聞いている内に、何とか使えるかも知れない、やってみようということで導入を決めたのだと言う。
つい先頃、工場長が若い人間に変わったことも、導入の決断をした大きな要因になったようだ。「ヤル気のある子なので、彼ならやってくれるかも知れないと思ったのです。いくらコンピュータが優れていても、要は使う側の人間に負うところが大きい。使いこなすんだという気持ちを持ち続けて、ねばり強くやっていくことが必要だと思います」
リテイルベーカリー繁盛シフト『@店舗』がピーターパンに届いたのが3月、キャンペーンということで1日講習が無料(通常は5万円+税)で受けられることになっていたので、4月4日、中心となる二人を連れて大阪のテクノバ鰍フ事務所で10時〜16時頃までの講習を受けた。そして現場に戻って、何度か話し合いをし、ビジュアルを見ながらそのスケジュールで行けるかどうかを検討していった。
「導入にあたって一番心配だったのは、実際に出力される帳票がそのまま使えるのかどうか、それと、従来のコンピュータに入っている入力情報を、そのまま繋いで使えるのかどうかということです。改めて入力し直すのではそれこそ無駄ですから」当初は使い方が不正確だったために不具合が起きたり、分からない部分もあったが、2〜3回メールでやり取りをし、手直しを加えることで現場に落とし込むことができたという。「汎用ソフトを使うときでもうまくいかないことがあり、使いこなさないままでお釈迦にする場合もあります。このソフトは何とか使いこなしたいという必要に迫られていたので、初期入力に2〜3週間かかりましたが、何とか使えるようになりました。私にしてはよく頑張ったと思います」
同社では約60アイテムのパンと学校給食用のパンを生産している。当初の設定は広川社長自身が行って大変だったが、基本ができれば後は事務ベースでこなしていける。今後は、月に4品程度の新製品を入力すれば済むようになるという。
同社がこのソフトを導入した一番の狙いは、成型の順番を明確にすること。同社においては、仕込み、成型、ドウコン入れまでの流れをきちんと把握するということが非常に重要な意味を持つのだという。 これまでは、生地が吹いてきたから次の工程に回してしまう、発酵が足りないということで手待ち時間ができる等の無駄が多かった。しかし、ソフトを使い始めてまだ数週間しか経っていないが、既に、@早朝の成型をしないでも済むようになってきたA一つ一つの所要時間が短くなってきたB途中の無駄なハンドリングがなくなってきた、等の成果が上がってきているのだという。
「当初の狙いだった、仕込み、成型、ドウコン入れまでの流れを把握することはある程度形になってきたように思います。それ以降の工程に関しては、これからデータを整理しながら、徐々に取り込んでいきたいと思っています。まだ導入したばかりで、最終工程までのデータ整理も十分でない状態ですが、それでも、かなり効率は良くなっているように思います。 感覚的には、2割程度の時間短縮が図れるのではないかと期待しています」
今回同社が導入したリテイルベーカリー繁盛シフト『@店舗』は、各社の仕様に合わせてオーダーメイドで作り上げる従来の『アドリフ』とは違い、名前の通り、標準的なリテイルベーカリーの設備を想定して作られたソフトだ。具体的にはミキサー2台、固定オーブン2台、ドーナツフライヤー1台、リバースシーター1台以内の設備を備えたリテイルベーカリーが対象になる。ピーターパンは前述の通り、卸しが主体のベーカリーで、設備的にもソフトに想定されているリテイルとは違っているが、それでも、使い方を工夫しながら、かなりの成果を挙げていることは間違いないようだ。
導入後の感想を広川社長は次のように語っている。「会社のデータをキチンと自分で入力しなければならないという一番最初のハードルを乗り越えれば、人間のイメージでは浮かばない生産形態が見えてきます。実際に使ってみて初めて分かることですが、出力したチャートを見て、それに鉛筆で自分の工夫を書き込んでいく内に、何か見えてくるものがありました」
|
|
|
食品産業新聞 2007年6月4日(月曜日) |
「アドリブ」出展 生産管理を最適化 テクノバ
テクノバ(大阪市浪速区)は、工場での作業合理化、人員配置の適正化に寄与する生産管理ソフト「アドリブ」や、リテールベーカリー向けのパッケージソフト「@店舗」などを出展する。
「アドリブ」jは、労働の非効率や過剰在庫といった問題を回避し、合理的な生産スケジュールによる効率的な作業を可能にするオーダーメイドソフト。MES(製造実行システム)機能の追加や、ネットワークにつなげることで、作業遅れの原因を統計的に分析してガントチャートに表示したり、離れた場所で複数の工場ラインの進捗を把握することが可能になる。
同ソフトは今までパン・菓子業界がメインユーザーであったが、今回の出展でターゲットを食品業界全体に広げることを目指す。
このほか、世界中で500以上の納入実績のある仕分けシステム「ディスポツール」(ツールボックスソフトウエア社)を出展。これは、各人がレールの上に設置したディスプレイの配色画面に従い、仕分ける量を顧客ごとに把握でき、正確な作業を可能にするシステム。
|
|
|
パンニュース 2007年(平成19年)5月22日(金曜日) |
各種生産管理ソフト テクノバ・2ホール 2G-19
「アドリブ」MES機能デモ
▽本社・大阪市浪速区元町3丁目1-1(鎌田ビル)電話06-6630-7812
テクノバの食品工場向けの”工場見える化生産管理ソフト”「アドリブ」は既に多数導入され確かな実績を上げている。
その背景には「アドリブ」がフローショップ生産のみでなく、バッチオーブンにも対応するように進化をとげたことにある。さらにスタンドアローンからLAN対応になり、大きなシステムの構築も可能になった。今回は現場と基幹システムを結ぶMES(製造実行システム)機能をデモンストレーションする。元来基幹システムは日管理で金と物の管理を主に、時分単位の日配商品などの細やかなスケジュール管理を必要とする生産管理には機能しないため、「現行の勘定系の基幹システムの生産管理機能に不満をお持ちの方にぜひ見ていただきたい」とコメントしている。
現場の状況を逐次入力することで、本部でほぼリアルタイムで現場の進捗状況を掌握できる。本社と工場をつなげば本社からでも工場の現状を”見える化”できる。また複数の工場をネットワークでつなげば互いの状況がわかるので、商品の相互補完を工場間で行なう場合極めて有効。
リテールベーカリーの売り上げと利益を増大する生産管理ソフト「@店舗」(アテンポ)
「@店舗」はリテールの販売パターンに合わせ、チャンスロスを防ぐなど売り上げを増大する生産スケジュールを容易に作成する”リテールベーカリー見える化ソフト”である。加えて製品データー管理、製品原価(材料+労務)、手粉にいたるすべての原材料管理、棚卸し管理、予定材料使用量管理、勤務シフト計画や人時生産性など経営をサポートする機能を満載している。同ソフトは、ミキサー2台、オーブン2台、ドーナッツフライヤー1台、リバースシーター1台の装備の範囲内であれば、ほとんどのベーカリーで使用でき、同社では"見える化”はお店の収益を確実に向上させると考えている。価格もリーズナブルに設定。またチェーンベーカリーに対しては本部で管理できるようなシステムの構築も可能だ。リテールベーカリーの近代経営化に力を発揮する。
「dispoTool」
「dispoTool(ディスポ・ツール)」は提携先のドイツ企業TOOLBOX(ツール・ボックス)社が開発した食品工場専用の仕分けソフト。既に世界中で500システム以上導入されている、パン工場仕分けシステムの世界標準的なシステムだ。
アドリブと接続することでサプライチェーンが構築できる。種まき法、買い物法のいずれでも使用できる。システムはコンピュータと頭上のレールに取り付けられたディスプレーで構成されているので、省スペースであるばかりでなく、顧客や製品変動に対してもフレキシブル。ディスプレーは作業者ごとに色分けされて表示されるので、狭い場所でも複数の作業者が仕分けを効率よく行なうことができる。操作は簡単で特別な知識は必要としない。
ペーパーレスでディスプレーの表示によって作業が行なわれるので、採用したばかりの作業者でもすぐに効率よく作業ができる。同社では「ぜひとも多くの方にブースで各ソフトの効用を実感してもらいたい」と期待を寄せている。
|
|
|
ブランスリー 4月号 平成19年3月20日 第7巻第9号 |
業界アンテナ リテールベーカリー向けの生産管理ソフト
リテールの労働環境はこのままでいいのか
リテールベーカリーの複雑な生産管理は、現場の長が、生産スケジュールの表を手書きで作成し、天候や気温なども考慮して、経験と勘で管理するというケースが多いが、このほど、リテールベーカリーに特化した生産管理ソフトが登場。開発したテクノバ、弘中泰雅社長らに話を聞いた。
― リテールベーカリー向けの生産管理ソフトを開発されたと聞きました。
弘中 私どもはこれまで量産ベーカリーの生産管理ソフトを開発・販売してきましたが、そのノウハウを生かして今回開発したのが、「@店舗」という、リテールベーカリー向けの生産管理ソフトです。
― 開発に踏み切った背景は?
弘中 リテールベーカリーは、毎日変化する販売環境の中で、販売機会ロスと過剰生産の狭間で、運営されていると思います。量産工場と異なり、販売ピークに合わせて製品をタイムリーに生産しなければ、いくら生産しても売れません。また、早く作りすぎれば、新鮮さが失われ、客離れが起きます。時間当たりの販売量の変化にあった生産スケジュールは、リテールベーカリー繁盛のカギになります。これがどれだけのベーカリーで正確に実践されているでしょうか。大手企業で最近パートなど、大きな労働環境の変化が起きています。リテールベーカリーの労働環境はkのままでよいのかという懸念も背景の一つです。
― 具体的に何ができますか?
弘中 主なものをあげると、まず生産計画、工程管理ができます。各製品の販売ピークに焼き上がり時間をあわせた、焼き上げ計画が容易に作成できます。例えば、「商品Aの販売のピークが、午前11時と午後5時で、商品Bの販売ピークが正午と午後3時で、商品C,D,E,F・・・の販売ピークが・・・」というように指定してやれば、指定された焼き上がり時間順に各商品を焼き上げるための全体の生産スケジュールを、各商品の各工程の所要時間や製パン設備の能力などに基づいて、自動的に正確に作成してくれます。同時に、その条件での1分ごとの仕事量を明示してくれます。
リテールベーカリーの場合、例えば急に雨が降り出したりして、販売環境が急変する場合もあるので、売れ行きをリアルタイムで判断しながら、その時々で追加生産、減産など、それ以降の生産スケジュールを簡単に変更できるようになっています。
こうして作成された生産スケジュールや必要人員は、表やグラフで視覚的に表示されますので、誰が見ても直感的に理解できます。ベーカリーの仕事の「見える化」です。
― リテールベーカリーの場合は、管理能力にたけた責任者が、常に厨房全体に気を配りながら、その時々の状況を判断し、フレキシブルに各スタッフに指示を出して、生産をこなすケースが多いと思いますが、それをコンピューターが、様々なデータをもとに自動的に行なってくれる、ということですね。
弘中 才能ある凄腕の管理者は、そう簡単に育つものではないし、経験と勘からの判断が常に正しいとは、言い切れないと思います。「@店舗」は、的確な判断を様々なデータからプログラムに導き出しますから、凄腕の管理者がいなくても、効率的な生産が可能になるし、凄腕の管理者の補佐役になれると考えております。
― その他にできることはありますか。
弘中 先ほど、1分ごとの仕事量が視覚的にわかるといいましたが、その情報と、あらかじめ入力したスタッフのシフト表とを比較しながら、人員配置を検討し、適切に修正することも簡単にできます。無理無駄のないワークシフトです。また、全原材料の使用量を算出し、原材料の無駄を省きます。指定した期間中の使用量も算出し、たな卸し機能もあります。安全在庫量設定により、材料の発注忘れを防ぎます。
― 今回のモバックショウに出展され、「@店舗」を発表されたとのことですが、反響はいかがでしたか。
弘中 多くの方に来場していただき、説明させていただきました。お蔭様で数社からご購入いただきました。
― ドイツのソフト開発会社ツール・ボックス社と提携し、同社の仕分けシステム「ディスポツール」のソフトウェアの日本での販売を始められましたね。
弘中 はい、お互いに協力して、販売していきたいと思っています。
― 商品仕分システムのソフトとはどのような商品ですか。
弘中 それはウルマー氏から説明します。
ウルマー 簡単にいうと、焼き上がって包装されたパンを、配送先別に仕分けるための指示を出すソフトです。
― どのような特徴があるのですか。
ウルマー 基本的な仕組みを説明すると順路に沿って、各配送先のスペースが並んでいて、配送先別に、商品ごとの納品数を表示する電光掲示版が掲げられています。一度に表示できる商品数は4つで、赤や緑など4つに色分けされています。作業者は、自分に割り当てられた色に示された製品数にしたがって、順路を進み、各納入先のスペースばんじゅうに、指定された数量を投入していきます。作業者ごとに色が決まっているのでわかりやすく、数字さえ読めれば誰にでもすぐに作業ができます。
― とても簡単ですね。
ウルマー 納品先の分だけのスぺーズがなくても、多重使用することで仕分けができ、省スペースが実現します。種まき方式、買い物方式のいずれの仕分方式でもできます。
― その他の特徴は?
ウルマー 当然、紙と鉛筆は必要ありませんので、仕分け作業が効率化され、仕分け作業に要する時間が短縮されます。パンの生産には、突発的な不具合が付き物ですが、生産管理のシステムと連動させれば、生産の情況に応じて、重要度の高い納品先に優先的にあ商品を投入したりするための指示を出すこともできます。 (問い合わせは テクノバ梶@06-630−7812 [email protected] )
|
|
|
パンニュース 2007年(平成19年)3月15日(木曜日) |
生産性と仕分け配送 リテイルベーカリー テクノバ社長 弘中泰雅氏
これまで量産製パン工場向けの生産管理ソフトを中心に販売してきたが、今回新たにリテイル向けの生産管理ソフト「@店舗/アテンポ」を開発し発売した。 「@店舗」は、リテイルベーカリーの生産性とチャンスロスなどを防ぐなどの販売パターンに合わせた生産スケジュールを簡単に作成するリテイルベーカリー向けの”見える化ソフト”だ。
リテイルの場合、量産工場と異なり、”勘や経験”に頼ってきた部分がある。(製パン技術には必要なことではある。)これらを”勘や経験”に頼るのではなく、きちっとした生産計画にすることで利益を生み出していく。意外と1個あたりのパンに人件費がいくらかかっているかを知っている店は少ないのではないだろうか。 リテイルの”見えづらいものを見えるもの”にし、店のあるべき姿を「見える化」していく。「@店舗」を導入し、「儲かる」リテイルベーカリーにとなって欲しい。
一方、ベーカリー専用仕分け配送管理システム「ディスポ・ツール」(同社提携先の独・ツールボックス社のウルマー氏が説明)は、製造・販売・輸送をいかに効率よく活用するかを考えたペーパーレスの配送システムだ。操作も簡単で新しい従業員も数時間でマスターできる。現在、世界22ヶ国に焼く500システム使用されており、17言語に対応。もちろん日本語にも対応できる。
|
|
|
ベーカーズタイムス 2006年(平成18年)10月10日 火曜日 |
サンジェルマンが生産性向上ソフト『アドリブ』を導入
潟Tンジェルマン(神奈川県川崎市、内藤信行社長)は9月4日、本社多摩川工場にテクノバ梶i大阪市、弘中泰雅社長)が開発した生産性向上ソフト『アドリブ』を導入した。今回導入した部門は多摩川工場内にある7部門中、食パン、菓子パン、食事パンの3部門で、10月から始まる新製品のラインに対応するための本格的な取り組みに着手した。同社では導入時の費用対効果の算定から、月間100万円の人件費削減を目標にしているが、今回の導入に至るデータ作成の段階でも、かなりのコスト削減効果が現れていることから、本格稼働後の数字にも大きな期待を寄せている。
サンジェルマンが生産性向上に着手
食パン・菓子パン・食事パンの3部門で生産性向上ソフトの『アドリブ』を導入
ソフト開発と導入サポートはテクノバ
現場での「見える化」を実現2本のラインを1本に集約化
潟Tンジェルマン(内藤信行社長)は、関東一円に「サンジェルマン」「フラマンドール」「ドゥマゴ」などのオーブンフレッシュベーカリー約100店舗を展開し、神奈川県川崎市にある本社多摩川工場では、各店舗へ供給するための様々な製品を製造している。
今回の生産性向上ソフト『アドリブ』を導入することになった経緯を、執行役員多摩川工場長の赤須正浩氏は次のように話す。「きっかけは、弊社の人事の人間がモバックに出展されていたテクノバ鰍フブースに立ち寄ったことからです。総務の視点から、人件費を削減出来ないかと考えて弘中社長に相談している内に、工場全体の見直しが必要では、ということになり、検討を始めたのです。
この工場は昭和45年に下高井戸工場を統合して集中化したもので、大量生産が出来るようにかなり大きなキャパをもった工場になっています。そしてその後、サンジェルマン各店舗での製造・販売にシフトして、工場での生産が大きく減ってきた今でも、工場内の生産ラインは以前のまま残っているという状態でした。 弘中社長に何度か工場を見てもらっている中で、『現状ではラインになっていない』という厳しいご指摘をいただき、また、『無駄なものを一つ一つ見直せば、宝の山だから、やってみませんか』というご提案を受けて、取り組みを開始することになったのです」導入を決定したのが今年の1月。予算取りをして、2月頃から今回導入することになった食パン、菓子パン、食事パン各部門の基礎データを作り始めた。
「弘中社長の指示に従って、内部で色々なデータを集めてお渡したのですが、弘中社長から『どうも納得いかない部分がある』という指摘を受けました」と話すのは企画担当統括マネージャーの望月重雄氏。指示通りにデータを集めているつもりでも、まだ建前なり、これまでの慣習なりに捕らわれてしまい、正確なデータになっていない部分が少なからずあったのだという。
「それで、4月頃から弘中社長ご自身に数回にわたって工場を見て頂き、その報告に沿って現場を見直し規格化を図りました。現場との色々なやりとりをしてソフトにも改良を加えて頂いたのですが、そういう柔軟な対応をしていただけるのも、弘中社長が現場のことを良く知っておられるからだと思います」実際の導入は9月4日。現在は、10月から始まる新製品導入に向けて、各ラインへの落とし込みを行い、『見える化』を図っているところだという。
9月4日のソフト導入までにも、既に様々な部分で効率化が図られている。例えば、これまで2本のラインで製造していた菓子パンラインを、1本に集約したが、製造上大きな問題は出なかったのだという。「大量生産していた時のままの工程でしたから、かなり無駄な部分がありました。取り組んでいる内に、現場から『前向きにやってみましょう』という声が出てきたことも、大きな成果だと思います」(望月氏)
バッチ生産の工程にも対応将来は各店への展開に期待
今回のソフト導入で期待している部分を赤須工場長は次のように話す。
「これまでは、あるラインにいる人はそのラインのことしか頭になく、そのラインの中だけで忙しい部署の応援をするという体制でした。しかし、ソフト導入によって『見える化』ができれば、3部門の違うライン、違う部署からでも応援体制がとれ、作業が平均化できます。実際にラインで作業している現場の人が、自分たちで問題点を見つけて改善していく。つまり、ラインの効率化をラインの人達が考えていけるようになれば大きな効果があがると考えています」また、望月統括マネージャーは、原材料の管理に関しても、次のような効果を期待しているという。
「これまでは現場で、原料が足りない、余りすぎている等の自体が幾度となく発生しています。店舗で集計し、指示書を書いて、配合表を付けて渡して管理していたわけですが、現場の都合で若干変更したり、その通り実行できていない部分もありました。しかし、今回のソフトでは、全てのラインで、どの製品にどの材料がどれだけ使われるかが一目瞭然です。原材料在庫の過不足を防ぐことが出来ます。更に、製品に何か問題が起こった時に、コンピュータでその製品に使われている材料を逆引きすれば、原因となる材料が瞬時に特定できます。原材料のトレーサビリティが求められている時代ですから、大きな強みとなるでしょう」 同工場は、大量生産時代から比べると生産額が半減している。現在はサンジェルマンの各店で販売する商品だけを生産しているため、ここまで工場生産の額が減少したわけだが、赤須工場長は将来展望を次のように語っている。
「この工場では平窯を並べてバッチ生産している商品もたくさんあります。今回のソフトは、ライン生産だけでなく、そういったバッチ生産についても対応できるように開発して頂きました。ですから、このソフトを手直しして、本社から関東一円の100店舗をオンラインで結べば、各店舗の生産能力が把握できるし、設備や人員の入れ替えによるシュミレーションも出来ます。つまり、サンジェルマン全体でのトータル的な生産管理も可能だと考えています。また、この工場自体の効率化が実現して稼働率が上がり、安全・安心のシステムが整ってくれば、現状のサンジェルマン各店への供給だけではなく、他の企業への製品供給も視野に入れることが出来ます」
今回ソフトを導入した食パン部門では2ラインで8種類、菓子パン部門は2ラインで16種類、食事パン部門は約50種類の商品を生産している。一カ月に約20種類の新商品がでることから、特注品や設備の入れ替えなどによる作業性などを事前にシュミレーションできる機能なども活用していきたいとしている。 同社では、今回のソフト導入による人件費コスト削減目標を、月間100万円に設定しているという。
|
|
|
ベーカーズタイムス 2006年(平成18年)9月10日 日曜日 |
寄稿 改正パート労働法
メキシコ、米国、トルコ、アイルランド、日本の順、実はこれはOECD(経済開発協力機構)発表の、先進国24カ国の相対貧困率(可処分所得が中央値の半分以下の世帯比率)の順番で、1位ブラジルは約20%、2位アメリカは約17%で5位日本は15.3%、24カ国平均は10.4%で、数字の上では1億総中流とは呼べなくなった。日本の格差拡大について、OECDは@非正規雇用の増加、A正規雇用者への保護が手厚すぎるとの見解だ。これを受けてか、厚生労働省はパート社員と正社員との賃金格差など是正するパート労働法を改正して処遇改善に取り組むことを決めた。正社員と同じような仕事をしているパート社員には同じ賃金を払うなどを明記し、企業への指導を強める。雇用均等分科会で議論し、来年通常国会にパート労働法改正案の提出を目指している。可決すれば、パート等の賃金は間違いなく増える。パート比率の高い産業への影響は必至である。人口減少による市場縮小の上に、労働市場は逼迫する。求人難と労務コスト増大のダブルパンチがパン産業に襲ってくる可能性がある。
|
|
|
ベーカーズタイムス 2006年(平成18年)3月10日 金曜日 |
ドイツパン工場視察紀行
マイスター制度を残しながら合理化ススムドイツの製パン工場
弘中泰雅
二月の前半、業務提携しているドイツのソフト企業ツールボックス社とのミーティングの為にドイツに行った。一週間余りの旅であったが、ツールボックス社のウルマー役員のお陰で、約1000kmも各地を走り回って、ドイツの製パン工場を7工場ほど視察できたので報告したい。これ等の会社を巡って、訪問した会社の多くが繁昌していると感じた。工場の建物はいずれも平均的には日本の工場の建物よりはしっかり作られているし、設備も比較的新しいものが多いようだ。主に夜間操業中に訪問したが、いずれの工場も明るく、日本の工場は手元の照度を確保する為に、照明器具を低めに設置してあるところが多いが、ドイツの工場では天井の高いところに照明器具があり、天井まで明るく全体的に清潔に見えた。最大の違いは床の材質で、出荷部門などは日本と同じくエポキシ塗装と思われるものが多かったが、パンの製造現場は明るい灰色のタイル張りで、丈夫で清潔に感じられた。いずれの工場も小麦粉など原材料はほとんどサイロから自動計量で供給され、工場内には粉袋、ダンボールなどはほとんど無かった。コンベアーは成型のところにわずかにあるくらいで、日本の工場のように工場中をコンベアーが走り回っていないので、工場が明るく開放的に感じられた。これは作られるパンのほとんどがハースブレッドの為、いわゆる天板や焼成ケースが不要なために、それらのコンベアーが無いことによるが、いずれにしても掃除がしやすい構造である。
最近日本では業界紙面でも、食品衛生がもっと大切な話題の一つであるが、ドイツでのそれは日本に比べて緩やかに感じられた。特に服装などは日本に比べて簡易で、日本の30年前の服装を想像していただければ、それに近い。ヘアーネットも無ければマスクもしていない。無論毛髪等の混入の問題はあると言っていた、国民性の違いか消費者が日本ほど神経質ではないのだろう。一つには環境的に冷涼で、腐敗や飛来昆虫が少ないことにもよると思うが、日本の工場は構造上あるいは運営上、異物購入を起こしやすい環境のまま、それを防ぐ為に厳しい管理をしていると言えなくもないだろう。一般的に日本の工場は、見た目ドイツの工場に比べて汚い、この点は一考の余地がある。
日本ではパン企業の利益が少ないという話をよく聞くが、ドイツのパン屋はその建屋や設備の新しさから察して、概して利益を出しているように感ずる。勿論消費規模の違いが大きい、古い資料で恐縮だが1995年のECの食用小麦粉消費は3500万トンで、当時の日本のそれは500万トンである。消費のベースであるECの人口は2億2500万人で日本の人口の約2倍であるので、一人当たりの消費量は3倍をくだらないであろう。しかも日本では麺類の消費が多いので実際には、5倍以上の開きがあるかもしれない。したがって店頭に並べられているパンの量はボリューム感がある。消費量に加えて、製品の価格が高い、いわゆる菓子パンはおよそ2ユーロ(日本円に換算して約280円)、無論かなり大振りであるが、それを差し引いてもかなり高い。その原因は大半のパンがスーパーではなくて、リテールベーカリーで売られており、マイスター制度との関わりもあろうが、価格が維持されているのであろう。現に早朝パン工場を訪問したときも、暗いうちから付設のショップにたくさんの人が、車に乗ってパンを買いに来ていた。無論この店はスリフトショップではなく、ドイツではパンは出来るだけ新鮮なものが求められるのである。したがって消費者は新鮮なパンを求めて朝早くからパン屋にやってくるのである。
今回訪れた工場の中で、スーパーが経営する工場もあった。これ等の工場は巨大で、日本の大手の工場に匹敵する規模である。日本では30年、40年以上たった大型のオーブンがかなり見られるが、こちらでは設備もほとんど最新鋭である。スーパー経営の工場は設備が最新鋭であるためもあろうが、工場情報の流失を懸念して、撮影は許可されなかった。その他の工場は従業員が50〜100名と思われる規模で、写真撮影に関しても、ツールボックスとの関係もあり大らかであった。これらは日本では経営的に最も厳しい規模である。それぞれの工場の規模を理解しょうとして、いろいろと質問したが余り小麦粉消費量や袋数をベースに工場の規模を表す慣例は無いようであった。工場もしくは会社の規模を訊ねると、たいていの工場では店の数、もしくは配送トラックの数が、規模の表現として返ってきた。これ等の会社の規模は概ね、10〜20店のリテールベーカリーと略同数のトラックを所有し自社の店で販売している。このほか若干スーパーなどで売る外販製品を作っているようだった。売上金額についてはほとんどがオーナー会社であるためか、返答をかわされた。
オランダ国境に近い人口25万に程度の市では、この上述の規模の企業が3〜4社存在し、これ等は一部オランダにも越境した、半径40km程度の販売エリアで入り乱れて商売をしているようであった。したがって人口30〜40万人の商圏で60〜80台のパン屋のトラックが走りまわっている計算になる。今回の移動中、大手スーパーマーケットのトラックと何台もすれ違ったので、大手ベーカリーの商品もかなりの量が売られているはずであるが、一人当たり消費量が日本の数倍もあるドイツだから、これだけのローカルベーカリーが存在しえるのであろう。
べーカリーの設備は日本でもなじみのメーカーのものが多く、連続オーブンはスーパーの大工場で見ただけであり、作業のほとんどはバッチ作業で、連続作業の設備は少なかった。作業そのものは昔ながらの作業で、パン作りそのもののは手作り中心で、生産効率は高いとは言いがたい。しかし原材料の計量設備や、仕分けのシステムなどの周辺設備は日本より、格段に進歩している。特に自動計量装置は、30年前ドイツを訪れた時にもあったし、今回全ての工場で導入されていた。これは段取り作業の効率、計量間違い、異物の混入には間違いなく効果があろう。既にトレーサビリティ(IFS,EU
1935/2004)の取り組みが始まって居り、それに伴うシステムの導入もすでに行われていた。業界として今後留意しておかなければならない部分であろう。
仕分けについては日本では、大手では大掛かりな固定の設備を導入して行っているが、柔軟性が低く、変化に対応し辛い、また設備が固定されているため掃除もしにくく、ごみがたまりやすく、昆虫の住処にもなりやすい。ドイツの工場では広々とした場所で、コンピューターを活用した仕分けが効率よく行われており、日本でもこのシステム導入を検討したほうが良い。またGPSとインターネットを活用した配送システムを車両に導入している企業もあった。これは生産システム、仕分けシステムなどと連動したしており、より顧客満足度の高い配送が行われていた。これ等についてより詳細な情報が必要な方、は弊社までご連絡を下さい。
久しぶりにドイツのベーカリーを訪問して、ドイツのパン産業が今後の日本のパン産業のあるべき姿だとは思わないが、マイスター制度を残しながらも、さすがに合理的な部分もあり、日本のベーカリーが参考にすべ基点は多々あると思った。多くの日本のベーカリーは低収益になやんでいる。国民性や制度、環境の違いはあるが、手作りを重んじる反面、利益の上がる商売、コストの下げかたなど合理的で、ドイツには日本のベーカリーに参考になるところもたくさんある。
|
|
|
ベーカーズタイムス 2005年(平成17年)12月10日 土曜日 |
白石食品が生産性向上に本格着手
複雑な菓子パンラインにも対応する生産性向上ソフト『アドリブ』を導入 開発と導入サポートはテクノバ
白石食品工業(株)(岩手県盛岡市、白石茂社長)が、テクノバ(株)(大阪市、弘中泰雅社長)が開発した食品工場の生産性向上ソフト『アドリブ』を導入し、菓子パンラインの生産性向上に本格的に着手した。
同社は現在、盛岡市にある本社工場のみで東北全域をカバーしており、平成16年度の年商は74億5千万円。取引先店は約4000店で、菓子パンのアイテムだけでも約200種類にのぼる。
今回のソフト導入の背景を、取締役生産部長の工藤善夫氏は次のように話す。「近年は人口が減少する一方でエリアが広がり、営業効率が悪くなってきています。また、大型量販店が次々に出店、その競合のあおりでパンの販売価格も下がってきています。このような経営環境の中で当社が利益を出していくためには、生産効率を上げていく以外にはありません」
しかし、同社は前述の通り一つの工場で多品種少量を製造しており、特に菓子パンラインは不連続なラインを適宜組み換えながら製造を行ってる状況だった。 このような複雑なラインで生産効率を追求することは不可能に近いと考えていたが、今年の2月、白石隆専務がモバックショウで、テクノバの弘中社長の話を聞き、直ちに検討するよう指示を出した。もともと白石社長・専務ともにコンピュータには明るく、その可能性を掴んだのだという。
そして4月に弘中氏からのプレゼンが行われ、5月に冷凍生地ラインで同ソフトを導入しているオイシスの高石工場を見学、6月にはソフト導入を決定した。 7〜9月にかけて現状のデータをとり、白石食品工業側からの様々な要望とすりあわせを行い、10月5日にまず自動化ラインからテスト運転を開始した。
「これまでは多品種少量生産ができるように色々工夫してラインを組み合わせてきていましたが、成形する順番のみが決まっている状態で、全体が把握できていなかったように思います。ソフトを使いこなすためには、まずラインを整理することから始めています。スタッフの気持ちも前向きになってきています。こういうことがないと、なかなか取りかかれなかったと思います」(工藤部長)
現在、工程の組み立てを行っているのは生産部製造一課係長の佐藤忍氏。「この工場では商品の改廃で週に7〜8アイテム、一カ月では40〜50アイテムが変更になります。これによって、人員の配置を適宜変更しなければなりません。量販店への納入時間と社員の出勤時間を考えて工程を決めていましたが、自分のいる成形の工程は見えますが、後の工程が見えていなかったので、これまでは無駄が多かったと思います。このソフトだと全体が一目で把握できるので、時間毎に変わる必要人数を把握し、前もって組み立てができるので、かなり効率がアップするだろうと考えています」
経理部経理課兼電算課次長の藤原一也氏は原材料のコスト削減にも期待しているという。「当社では約2千種類の原材料を使っていますが、これまではその使用予定状況が原材料のアイテム別にわかる仕組みができていませんでした。アドリブは原材料の使用予定状況が一目でわかる機能も備えていますから、今後は材料の使い込み・使いすぎ等もその都度チェックできます。大手のソフトメーカーからも色々ご提案をいただきましたが、パン製造の現場がわからないと、適切に機能するソフトが組めません。弘中社長は、パン作りの工程を熟知しておられるので、色々な要望を確実に処理していただけます」
工程を統括している生産部製造一課課長の天沼巧氏は、スタッフのモラールアップに期待を寄せる。「ソフト導入で部署毎の人員配置や出勤時間の見直しが行えます。そして、余った時間を有効に活用することができるようになりますが、その為には従業員のレベルも同時に上げていくことが必要です。これから順次シュミレーションを行い、ソフトを現場に適応できるようにバーションアップして一つ一つ課題をクリアしていきますが、同時に、作業員のレベルアップを図っていき、来年4月を目途に本格稼働できればと思っています」
「厳しい経営環境を打破するためには意識改革が必要ですが、今回の導入は丁度いいタイミングではなかったかと思います。4月から忙しい時期に入りますから、2月3月で何とかシュミレーションを終えて、その時期に備えたいと考えています」(工藤部長)
*テクノバ鰍ヘ食品工場向け生産スケジューリングシステムの開発販売およびコンサルティングの会社。
電話番号06(6630)7812 http://www.technova.ne.jp/
|
|
|
パンニュース 2005年(平成17年)7月25日 月曜日 |
テクノバ 独のソフトウエア会社
ツールボックスと提携
|
|
|
ベーカーズタイムス 平成17年7月10日 日曜日 |
テクノバがドイツのシステムパートナーに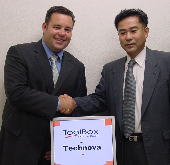
テクノバ(株)(大阪市浪速区弘中泰雅社長)はドイツのソフトウエア会社ツールボックス(GmbH
Eschweilier, Mr.T.Mertes社長)と販売と市場調査のパートナーシップを結ぶことになった。2005年5月に、ツールボックスのオーナー社長
Mr.Mertesと国際営業担当のMr.Ulmerがテクノバを訪れ今回の提携になった。
両者は、日欧の製パン・食品加工産業が効率化と最適にカスタマイズされたソフトウエアを捜し求めており、テクノバとツールボックスのそれぞれのソフトウエアが成熟したソリューションであると同時に、これ等は相互の市場で認められる顧客志向のソフトウエアであることを確認した。
「今回の販売パートナーシップはテクノバの国際志向の第一歩であり、我々のソリューションの有効性が国際的に認められてうれしい」とテクノバの弘中社長は述べた。テクノバとツールボックスのソリューションは相互に完全に補完する。今回の提携によりテクノバは従来の生産性向上のソリューションに加えて、ツールボックス社の仕分けシステムやGPRS機能を持つ配送システムも販売していく。
これ等のソフトウエアは既に日本国内の数社に紹介され、関係者に興味をもたれている。テクノバのソフトウエアも今後IBAなどの海外のベーキングショウで紹介するなど、これを機会に全世界を市場として開拓していく予定である。 |
|
|
ブランスリー5月号 平成17年5月 |
人口減と労働力不足 生産性向上がカギ
これまで日本の人口はずっと増えてきたので、食品産業の売上もずっと伸びてきた。売上が伸びてきたので生産性について余り考えてこなかった。しかしこれからは人口が減っていく。人口減によるマーケットの縮小が起こってくる。必然的に食品産業全体の売上は減っていく。したがって生産性についてシビアに考えざるを得なくなる。
また、労働人口の減少により、労働力不足がおこってくる。企業は労働力確保に苦労する時代に直面するだろう。したがって、生産性を是が非でも向上させなければならなくなる。
私どもが開発した「アドリブ」は、生産設備や労働量などのリソースを最大限に生かす生産計画が立てられるソフトだ。作業量と投入労働量が簡単に比較できるので、目で見る菅理ができ無駄な人件費を発生させない。工場の生産能力に合わせた生産計画が誰にでも立てられる。
また、納期遅れを起こさず、過剰在庫を発生させず、チャンスロスを起こさない生産計画が立てられる。使用原材料を算出するので、適正な原材料の使用が確認でき、無駄な原材料使用が防げる。 |
|
|
ベーカーズタイムス 平成17年4月10日 日曜日 |
モバックセミナー/テクノバ
『工場は宝の山』
多品種。複数ラインの生産性向上」
テクノバ(株)の弘中泰雅社長は「工場は宝の山、冷凍工場はもっと利益が出る。多品種生産、複数ラインにおける生産性向上のポイント」というテーマで講演を行った。以下はその要旨
◇ ◇
昨年、(株)オイシスの高石工場に弊社の「アドリブ」という生産計画ソフトを導入していただき、ベーカーズタイムス紙に取り上げていただきました。今回はこのモデルを例に、複数のラインを持つ冷凍生地工場の生産性向上についてご説明します。
冷凍工場の生産に実際に携わっておられる方は、@計画生産ができるので勤務時間が抑制できるA規格が確立しているB適正在庫の維持ができるC出荷量変動に対応できるDまとめて生産できるので、生産効率が上がり資材菅理等も容易等等をお考えのようでしたが、しかし現実は「ナルハズ」といったことで、問題がたくさんあるようです。
労働生産性の指標としては、人時あたりの生産金額がよく用いられます。したがって、労働生産性は総労働時間に大きく影響を受けます。総労働時間は人数×労働時間であり、これに基づいて人件費が発生します。しかし、支払われた人件費に対する時間のすべてが直接的な生産活動に使われていないのが現実です。例えば、手待ち時間、手空き時間、機械のトラブル等ですが、労働生産性を向上させるためには、これらの間接労働時間を削減することが必要になります。
まず手待ち時間ですが、一つのラインで多くの製品を作ると、作る製品によって@フロアタイムが終わっていないので分割できないAホイロが出ないのでオーブンに入れられない等の手待ち時間が出来てしまいます。これを無理やり詰めても、次の工程で手待ちが出来たり製品に影響したりします。しかし単に、作る製品の順序を変えることによってトータルの生産時間が各段に短くなります。
HMなどを使用した成形工程の複雑な冷凍生地ラインは、労働集約型で作業者の人数はアイテムごとに大きく変動します。そして、複数のラインを同じ部署にそろえることが多く、作業員が共用になっていることが多いので、作業者はアイテム毎に移動します。
例えば2本の生産ラインを持ち、部門の作業者が8名の冷凍工場があるとします。5人必要な製品Aを3種類、3人必要な製品Bを4種類生産しなければならないときに、2本のラインで必要な作業者は6人〜10人になります。6人でこなせるときは2人が手空きになり、10人必要な場合は、生産速度を落とすか、断続的な生産になってしまします。
この時に、生産する製品の順序を変えることで部門8人の作業員でトラブルなく生産することが出来ます。以前なら、生産性が悪くなるか、過剰な人員10名を抱えることになります。これを目に見える形に示してくれるのが生産計画ソフト「アドリブ」です。アドリブは作業量と供給労働量の差が一目瞭然に把握できます。
この他にも、生産能力と出荷状況を見ながら長期生産在庫管理や、当日の総生産量、総在庫金額、製品ごとの在庫量や当日の生産予定数なども確認できます。また、使用材料情報では全ての材料の使用量と使用金額が任意の期間に対して算出されますから、材料原価比率も算定できますし、製品編集画面では製品の生産要素の菅理を行います。これがすなわち製品標準書にあたり、この資料を作成するだけでも作業が規格化され生産性が向上します。
実際にアドリブを導入していただいたオイシスでの主な効果をベーカーズタイムス紙から抜き出して見ると、次のような項目が挙げられています。
@見えない無駄が見えてきたA後追いのデーターでなく、明日を改善するデーターが一括されたB効率の悪い現象を示すだけでなく対策ができるC人員の適正配置が容易になったD作業の基礎データの見直しができるE生産時間に対する現場の意識が変わってきたF問題と課題が具体的に見える等々
「ウチの工場の問題は生産性が低いことだ」という言葉をよく耳にします。しかし、生産性が低いということは結果であり、問題でありません。生産性低下を引き起こす原因を見つけだして解決することが大切なのです。生産性の向上には3つのポイントがあります。1つは手待ち時間の削減。2つ目は手空きの削減。3つ目は雑多な生産を阻害するトラブルの解消です。そして問題は、これらを改善する具体的な手段・方法を持っているかどうかです。
問題を見つけ、コンピューターの戦略的利用など、これに取り組む実行力さえあれば、「工場は間違いなく宝の山」に変わります。 |
|
|
パンニュース 2005年(平成17年)2月15日(火曜日) |
「アドリブ」で生産性向上
テクノバ・2号館219
パン工場を儲かる体質に移行
▽大阪市浪速区元町3-1-1 鎌田ビル 06-6630-7812
テクノバは製パン工場の生産性向上ソフト「アッチェレランド」を4年前からパン業界に提案し、大きな反響を呼び、大手ベーカリーでも採用、着々と実績を増やしている。今回のモバックショウでは「アッチェレランド」の機能をさらに広げたソフト「アドリブ」を紹介する。既に大手ベーカリーでも採用され好調だ。
生産計画ソフト「アドリブ」
@工場の生産能力に合わせた生産計画が誰にでも出来る。
A納期遅れを起こさず、過剰在庫を発生させず、チャンスロスを起こさない生 産計画が立てられる。
B生産設備や労働量などのリソースを最大限に生かす生産計画が立てられる。
C作業量と投入労働量が簡単に比較できるので、目で見る管理が出来る。その ため無駄な人件費が発生しない。
D使用原材料を算出するので、適正な原材料を使っていることが確認でき、無 駄な原材料使用を防ぐことが出来る。
天候や流行、催事などの要因により需要の変動が大きい冷凍食品、冷凍パン生 地、アイスクリーム、和洋菓子、フィリング類、加工食品などの冷凍品や日持ち商品は在庫過剰と欠品によるチャンスロスとの狭間で悩みながら生産しているのが実情である。
特に素材メーカーにこの問題が多い。日配商品と違って若干日持ちするため出荷日と生産日との間に生産の自由度があるので生産計画の立て方によって工場の生産効率が大きく変わる可能性がある。これは適正在庫はいかにあるべきかを解決するための生産計画作成ソフトである。
テクノバ「アドリブ」はアイテム毎に長期生産計画に見込まれる受注や確定受注などをいれてごとの生産数量を設定する。生産や在庫の状況をグラフで表示するので生産、在庫状況を目で感覚的に進めることができる。在庫が不足した場合は警告を発することで対応できる。
ラインごとの労働量だけでなく複数ラインや工場全体の必要労働量と供給労働量が表示されるので、無駄なく労働力を割り振りしたり、生産順を変えたりして必要労働力と供給労働力のバランスを取れる。
生産性向上スケジューラー「アッチェレランド」
従来から人気の生産性向上スケジューラーソフト「アッチェレランド」も中堅リティルベーカリーに人気があって引き合いも多い。
生産性向上コンサルティング
テクノバは食品工場の生産性向上コンサルタントをおこなっている。出荷金額数億円から200億円のコンサルティングの実績がある。対象は食品工場のほとんどの領域にわたり、例えば「コープこうべ」の場合では六甲アイランド工場で扱う、和洋菓子、ベーカリー、製麺、豆腐、納豆などの各部門を対象とした。またテクノバは大阪府中小企業支援センターのアドバイザーとして登録されている。 |
|
|
ベーカーズタイムス 平成17年2月10日 |
冷凍生地工場の生産性を一挙に向上させるアドリブ
食品工場の生産性向上を支援するテクノバ(株)は、前回のモバックで紹介した、理想的な生産順を計画するスケジューラー「アッチェレランド」(このソフトは導入6ヶ月間で、食パンラインにおいて10%以上の生産性を向上した実績を持つ)の他に、新しく開発された生産計画ソフト『アドリブ』を出展する。
従来の生産計画ソフトは納期に間に合うようにただ生産計画を立てることが目的だったが、本ソフトは従来のソフトで扱えなかった、生産活動の中で生ずる作業者の手待ち、手空きの状態を分かりやすくグラフで表示するので、生産状況を目で見て、合理的な生産計画が立てられる。
この全く新しい生産計画ソフトは、一目で作業の状況が分かるので、他のラインの必要人員などを考慮にいれて、生産順の組合せの変更時間調整を行って、効率の良い生産計画がたてられ、生産性の向上が実現できる。
また一括入力できる作業者の勤務状況が一目で分かるヒストグラムや、加えて材料の使用量、原価菅理も随時できる。更に生産予定だけでなく、出荷予定も計画して将来の製品在庫の菅理もグラフ上で確認できるので冷凍生地で発生しがちな在庫量の圧縮など極力削減できる。
従来、材料の価格変動に対して製品の材料原価をリアルタイムで把握することは難しく、製品開発時の材料原価で間に合わせているのが現状であったが、本ソフトではリアルタイムで製品材料原価を確認できる。
更に、生産計画だけでなく、冷凍工場の生産性を向上する全ての機能が含まれている。カスタマイズで冷凍工場以外の他の生産形態に変更することもできる。
このほかテクノバ(株)では現場主義の生産性向上のコンサルティングをおこなっており、多くの工場で実績を上げてきた。これらについてもブースで説明を行う。
◆モバックセミナー セッション12
テクノバ(株)はモバックショウのモバックセミナーにおいて「冷凍工場の目で見る生産計画ソフト『アドリブ』」と題し、ホールセールベーカリー、リティルベーカリーのセントラル工場などを対象に対象に、冷凍生地ライン用の生産状況が目で見て簡単にわかり、生産効率を向上し、製品在庫、資材菅理が容易にできる生産計画ソフトを紹介する。
【内容】製パン業界の知識と電機産業の生産性のノウハウを基に生まれた生産計画ソフト「アドリブ」を使用して、冷凍工場の生産性の向上に取り組む、導入事例も紹介し、冷凍工場の生産性の向上を分かりやすく伝授する。 |
|
|
ベーカーズタイムス 平成17年2月10日 |
オイシス高石工場の冷凍生地ラインで
テクノバの生産性向上用ソフトを導入
大手製パン企業では初めての導入
潟Iイシス(本部=伊丹市池尻、池野忠司社長)が昨年、テクノバ梶i弘中泰雅社長)の開発した生産性向上ソフト「アドリブ」を導入、11月から稼働を開始した。これまで弊紙でも、業務用パンメーカーのオリエンタルベーカリーやコープ神戸六甲アイランド食品工場の生産性向上への取り組みを紹介してきたが、日本パン工業会所属の大手製パン企業での導入は初めてのこと。まだ、導入して間もないが、今回の導入に関して直接指揮を執っている潟Iイシス取締役生産本部長の仲修氏、高石工場生産部主任の新美秀己氏、高石工場パン事業部の寺司武広氏の3氏に、その進捗状況を聞いた。
――導入のきっかけは?
仲 当社は色々な販売先、色々な受注形態があり、それを生産する工場では24時間稼働の複雑な仕組みを抱えています。これまではそれらをこなすために経験の中から管理工程を作ってきていましたが、新しい管理に役立つ仕組みや社員のモチベーションがあがるような仕組みが作れないものかとずっと考えていました。
そんな時、弘中社長から生産性向上ソフト『アッチェレランド』のご提案をいただきました。もちろん費用対効果が前提にありますが、まずはパン工場の中でも数少ない計画生産が可能な冷凍生地ラインに生産計画ソフト『アドリブ』を導入できないだろうかと考えたのです。
計画生産とはいうものの、品種が多く経験則では対応し切れていません。このアドリブを導入することで、経験則ではないやり方を考えることができると思いましたし、若い社員に生産効率をこれまでと違う視点で捉えてもらえれば、他のデリカ、惣菜ラインにも役立っていくと期待して導入することにしました。
――実際の導入はいつからですか?
仲 昨年の2月ぐらいから準備にかかり、契約は4月。そこから現場でのヒヤリングを開始して、実際にソフトを動かし始めたのが11月からです。
――稼働してからまだ3カ月目ですが、印象は?
仲 これまでの経験でやっていた時には、無駄と分からないことが多かったですし、分かっていてもやむを得ないと思ってきました。しかし、原材料のコストダウンはもちろんですが、労働時間の短縮がより大きい部分。これを目に見える形にして実感が湧けば、対応の仕方が変わってきます。
新美 導入して、これまで物事をいかに科学的に見ていなかったかがよく分かりました。生産する生地の品種によって速度が違うのに、アイテム毎に捉えているつもりでいました。それを実際に数字で表現されると、計算では半分のスピードでやっていたことが分かりかなり戸惑いました。しかし、理解できればこのツールによって、改善する方法を見つけだしていくことが出来ます。
仲 当社の作業基準は、総労働時間、ロス管理などのデータベースを手作業とパソコンで管理していました。ただ、一つ一つはありますが、全体を把握するには経験と勘に頼っていた部分があります。但しそれでは、後追いのデータは付けられるのですが、明日をどうするということが考えにくい。今回のアドリブはスケジューリングと共に、在庫管理、計画生産、原材料使用状況まで分かるように作っていただいているので、他にも色々使えると考えています。
新美 現状が目で見られる状態になっているので、結果の後追いではなく、この時間にはこの人員でいけると判断できるようになりました。いかに必要な人員を均等に配分するかが一つの大きなポイントだと思っています。
一週間分の工程計画を立て、終了時間も週間単位で同じ時間に終われるようにしたい。将来的には余剰人員も減らすことが出来ると思います。
――実際にはどのように活用されているのですか?
新美 工程毎の終了予定の時刻を表示し、実際の終了時刻を記入させます。そして、ズレたらその理由を必ず記入させるようにします。言い訳めいたものも多いのですが、それでも理由を一生懸命考えるので、問題点が浮き彫りになってきます。 まだ1分2分のズレを気にする人と、30分ズレないとそう気にとめない人など、人によって温度差はありますが、今はトータルの誤差が30分位になってきました。今後は1分2分を追求していこうと思っています。
仲 デイリーフーズの業務をしているところは作業が複雑で、効率が悪くなる理由を幾らでも挙げられます。ただ、理由は挙げられても、これまではその対策が打てなかった。今回のスケジューラーによって計画生産し、作業分析が出来ると、一人一人のスキルを上げることができ、余剰人員に別の仕事をしてもらうことができます。当然、ライン全体のレベルが格段に上がると考えています。
それから今までの基礎データを見直し、入れ替えることも可能ですから、これで、次の段階に行くことが出来ます。例えば、機械の使い方、配合などを含めて見直すことが出来るのです。
寺司 今までの経験で作ってきたスケジュールは、細かいもので5分刻みでしたが、アドリブなら1分単位でスケジューリングできます。1アイテムで1〜2分でも、トータルでは30〜40分の短縮になる事が分かり、かなり現場の意識が変わってきたようです。無駄が数字で見れると意識が変わるのですね。
新美 日報を毎日確認し、週に1回データをまとめて検討し、次の週の目標(計画)を提示します。日報に書かれていることが言い訳でも、管理する側にとっては良い情報、データになります。現在の目標を達成し、次のノルマが厳しくなって目標が達成できなくなると、次の新しい提案が出てくると思いますから、それを期待しています。
――これまで改善された具体的な事例はありますか?
寺司 玉生地ラインで計画より1時間遅れるようになり、担当者が必死に遅れる理由を日報に書いてきました。生地が不安定でベタつくという理由が主だったので、機械メーカーと検討し機械の改善を行って遅れがなくなりました。
問題と課題が具体的に見えるので、それを潰すことで一つずつ改善できます。
仲 弊社では作業の準備や手配、手待ち時間を間接時間と言っていますが、要はこれが無駄な時間です。11月は1日95時間でしたが12月は85時間になりました。例えば時給を千円とすれば1日1万円減ったことになります。たかがと思われるかも知れませんが、年間では300万円の削減です。300万円の生地を捨てるのは大変だと思いますが、300万円分の時間は簡単に捨てていた。この意識が大事だと思います。
この意識が全工場に広がり、8工場で水平展開できれば、金額的にもとても大きいものになります。
――冷凍生地ラインで削減目標はどの位ですか?
新美 トータルで月間150万円のコストダウンを目標にしています。
仲 思考能力が停止するような環境では駄目だと思います。これを是正する環境を作っていけば、自ずと効果が出てくると思っています。導入直後でも既に月間30万円弱のコストダウンが出来ているわけですから。
|
|
|
ベーカーズタイムス 平成16年4月10日 土曜日 |
転換期を迎える老舗パンメーカー亀井堂
米飯工場新設を契機にして会社全体の体質改善に着手
−省略−
「私が社長に就任してからは、比較的若い人材も登用するようにしてきましたが、それでもまだ古い体質が抜け切れません。古いものが全て悪いというわけではありませんが、内部にどっぷり浸かっていると、変革すべき部分が見えなくなっている場合があります。
それから、部分的にはここを改善したらどうかというのは出てきますが、トータルとしてそれがどのように繋がっていくのか分かりにくい、それを目に見える形にして、従業員と一緒に全社で取り組んでいく必要があると思っていました。 それで今回、テクノバ鰍フ弘中泰雅氏にじっくりとパン工場を見てもらい、課題をいくつか提示していただくことにしたのです。」
地原氏は弘中氏の生産性向上に関する考え方に共感を持っていて、ベーカーズタイムス紙に掲載されたコープ神戸六甲アイランド工場の記事を見て、具体的に動く事を決めたようだ。
「先日2日間、朝から夜中まで、そして夕方から朝まで、ずっと工場を見てもらい、いろいろな指摘をもらいました。これらを私が考える新生亀井堂のコンセプトとすりあわせて、従業員と一緒に一つ一つ解決していくつもりです。(地原社長)考えているだけでなく、いつ動き出すのかで未来が決まる。動き始めた亀井堂の今後に期待したい。
|
|
|
ベーカーズタイムス 平成16年1月10日 土曜日 |
「管理から変革へ」をテーマに全社を挙げて生産性向上に取り組む
コープこうべ六甲アイランド食品工場
あらゆる食品メーカーにとって、「衛生管理」と「生産性向上」の2点が、現在の最重要課題と言っても過言ではない。今回は、その内の一つでもある「生産性向上」を自社の最重要点課題に掲げ、三年前から全社を挙げて取り組みを開始したコープこうべ六甲アイランド食品工場(神戸市東灘区)の事例を紹介する。
コープこうべの自己生産事業のルーツは、神戸消費組合・灘購買組合共同で「みそ・しょうゆ」を醸造した大正13年にまでさかのぼる。その後、組合員に本当に必要なものを自分たちの手で生産するという姿勢から、パン・菓子、麺、豆腐など、次々に新たな品目の生産を開始。そして、量質ともに一層の充実を図るために、昭和63年、現在の六甲アイランド食品工場を稼動した。
この工場では現在、日常生産と正月餅やクリスマス等の催事商品を含め、約500アイテムの商品を生産しており、コープこうべ各店舗、共同購入や41店舗のインストアベーカリー(2002年現在)の他、Kネット連帯機構加盟の京都、滋賀、奈良、四国、新潟、山口の各生協にも供給。その出荷額は約150億円にものぼっている。
コープこうべの「安全」に対する取り組みには長い歴史があり、@安全・安心A美味しさB素材を厳選C新鮮さのこだわりD環境への配慮 という五つのスローガンのもと、疑わしい添加物をいち早く排除し、細菌検査をはじめとする徹底した衛生管理体制は社会的にも評価されている。
社内の意識改革を図り生産性向上のための土台作り
そのコープこうべが今回、食品メーカーのもう一つの重要課題である「生産性向上」に全社を挙げて取り組み始めた背景を、牛島康治工場長は次のように話している。
「ここはもともと組合員のために自己生産して、店舗や共同購入で販売する形態なので、競合が無く、最盛期はコープこうべ全体で年商3700億円までいっていました。しかし、最近のニーズの多様化等によって様々な競合が生まれ、少しずつ厳しい状況になってきていました。また、この工場も15年前に作ったコープ160店に供給する少品種大量生産型の工場で、近年の多品種少ロットニーズに対応しきれなくなっていました。
それで、三年前から生産性の向上を最優先課題に掲げ、全社を挙げて取り組みを開始したのです。」そして、社内で様々な取り組みを模索しているところに、モバック会場で行われるセミナーに、潟eクノバの弘中泰雅の『アッチェレランド(生産性向上ソフト)による生産性向上』の講演があることを知り、その講演を聴きに出かけたのだという。
「講演を聴いて、初めはソフトを導入すれば何とかなるのではないかと思ってスケジューラー導入の検討をしましたが、色々な話を進めていく中で、そのソフトを導入するための土台作りから始めないと何の効果も得られないという結論に達したのです。それで、弘中先生に工場を見ていただき、チーフクラスの人間に弘中先生の考え方や視点を学ばせようと、コンサルタントをお願いすることにしたんです」(牛島工場長)
牛島工場長が、ソフト導入の段階ではないと判断した最大の要因が、社内の職員の意識だったようだ。「供給しているのが自分たちの商品しかないという甘えがあり、外の厳しい状況を認識できない風土があります。多品種少ロットに対応できないのも、設備・機械のせいにしてしまいがちで、いつの間にか自らの工夫を忘れていたのです。
他のパンメーカーの品質もかなり向上しています。仕入れ商品の方がメリットがあればそれに移行する。つまり、自工製品の必要性さえ問われているのです。今これに取り組まなければ生き残ることはできません。それで、外部の事例や考え方を学び、事実を認めて変革していこうということで、弘中先生を中心に取り組みを始めたのです」
具体的には9月の中旬から約2ヶ月間かけて、弘中氏と一緒に工場内の全行程をチェックした。終日稼動している工場なので、そのチェックは深夜になることも珍しくなかったそうだが、生産ラインの考え方から細かいところではラックの動かし方まで、基本的な部分を全てチェックし、逐次改善していった。「本来は私がやるべき仕事なのですが、弘中先生には直接現場に入って問題点を指摘していただき、その都度幾つかの具体的な改善策の事例を提示していただきました」(牛島工場長)
現場担当の田口孝志課長も「単なる指摘だけなら多くのコンサルタントの先生がしてくださるのですが、弘中先生は現場のこともよく分かっておられるので、専門的な立場から具体的な改善策の事例を提示していただける。これが現場の人達との信頼関係を築き、良い方向に進んでいるのだと思います。
具体的な効果としては、マネージャーやチーフクラスの人間の意識が変わってきたことです。ラインのどこが滞っていて、どういうところを改善しなければならないのかを、自分達で見つけることができるようになりました。職場内でもマネージャーやチーフの間で、自然に生産性についての論議が出るようになっています。
現場に入り込んでしまうと、自分達ではなかなか問題点に気づかないものですが、今回の指導によって、問題点の見つけ方、いわゆる『気づき』を実践できる人間が出てきたということです。今後は、こういう人間を一人でも多く育てていくことが必要だと思っています」と話していた。
アッチェレランドの導入も検討 改善実績を人事考課にも反映
コープこうべは昨年の4月、業務の効率化を図るために別会社として潟Rープベーカリーを立ち上げた。六甲アイランド食品工場の従業員470人の内の420人がこの別会社の委託社員やパートで構成され、その人達が直接製造に携わっている。
「少し複雑な労務構成ですが、コープ本体では難しかった若い技術者の採用・育成が積極的にできるようになりました。この機会に基本的な生産管理の考え方をOJTを通じて社内に浸透させ、一人ずつ考え方を共有できる人間を増やしていこうと思っています。
現在でも生産事業では何とか10%のネットを残せていますが、この利益を残しながら組織や仕事の変革を実施していくことが必要です。
今回の取り組みで『これまでのようなドンブリ勘定的な工程分析では通用しない。具体的で細かい分析による問題点の抽出と改善が必要だ』ということを気づかせていただきました。今後はこのベースを100として、ここから更に生産性を上げ、実績に応じて人事考課にも反映させていかなければならないと思っています」(牛島工場長)
今の同工場のテーマは『管理から変革』。昨年より今年、先月より今月、昨日より今日と何か変革していくことを実践している。同工場では3年前から全職員を対象に、ロス削減や工程の改善などについての改善提案運動を実施し、毎年300〜500件の提案が出ている。
「今年は2月に実施する予定ですが、今回の取り組みの後ですから、どんな提案が出てくるか今から楽しみにしているんです。提案内容については、どんな小さなことでも構わないんです。それらを検討し、現場にフィードバックしていけば、必ず効果は現れてくると思います。
そして、変革していこうという社内風土が高まってきたら、本当の生産性向上を図るために、実験的に1ラインにソフトを導入して成功例を作り、それを更に改善していきながら、委託の人達の人事制度にも結びつけていきたいと思っています」(牛島工場長)
最後に牛島工場長は次のように強調した。
「私達の最大の目的は『組合員の満足』です。そのために、常に品質向上と生産性向上を図り、安全で安心できる商品を安定的に供給し続けていかなければならないと思っています」
お問合せ |
|
|
ブランスリー7月号 平成15年7月より連載中 |
生産性よもやま話 TECHNOVA'S EYE VIEW |
|
|
日本パン菓子新聞 平成15年5月15日(木) |
パン技研 講習会
パン工場のIT化で生産性の向上と労働コスト削減を実現
(社)パン技術研究所の研究調査部は4月14日、東京・西葛西の同研究所で、「生産性の向上」と題する講演会を開催した。講師は、生産コストの削減を追求するパン生産管理ソフト「アッチェレランド」を開発したテクノバ鰍フ弘中泰雅社長。』受講は製パン各社、関連企業などから32名参加した。
【講演要旨】
パン産業が主要産業の中で最も生産性が低い理由は、産業別労働生産性の伸び率の低さや、主要産業中一番高い直接労働費、他産業と比べても極めて高い人件費率など、統計上の歴然とした事実に現れている。
1975年と98年の主要産業の労働生産性の伸び率を比較すると、全産業平均の約3倍に対し、食品製造業は1.29倍で年率1%も生産性が向上していない。産業別の人件費率もパン製造業は極めて高いのも、従業員に多くの賃金を支払っているという意味ではなく、全体の生産性が低いため、見かけ上高くなっているだけだ。
また日本経済の停滞とデフレにより、特に冷凍パン、冷生地輸入や低賃金・低コストなど、中国が生産拠点、日本からの技術流入の場として台頭している。国内においても、人口減少に伴うパン消費量の低下、パン生産の減少、高賃金・高コストなど、製パン産業を取り巻く状況は厳しくなる一方だ。このように、限界的な市場を皆で奪い合っている事態を避けるには、速やかに労働生産性の向上に取り組まなければならない。
パンの生産性が低いのは、今までのパン工場は、厳しい国際競争にさらされることなく、需要の増大・量的な対応のみに終始し、設備投資主導の生産工場を展開していたからだろう。実態は、@標準作業方法を無視、Aアイドル時間(手待ち時間)を積み重ね、B機械設備の標準運転条件の不徹底、C標準作業ペースが無い等、生産工学的な要素を取り入れていない。以上から、今後生産を向上させるには、アウトプットに対応するインプットの相対的関係を改善させなくてはいけない。
しかし、単純に生産性の高い電気産業のシステムをパン工場に取り入れるだけでは不十分で、パン製造の特性を考慮する必要がある。日配商品であるパンは、生地仕込み、発酵、成形、焼成、仕上げなど多工程で構成され、作業の所要時間も、パンの種類や生産数によって大きく変動してします。これが、多品種生産ラインの生産管理を極めて難しいものとしている。
多品種を生産するには、作る順番が問題となる。多品種を製造する複雑な作業は、実際は手待ち時間が多く、隙間だらけ。しかし制約条件(製造条件、製品仕様、出荷時間など)を守って、工程に流す順序をリソース(生産設備や人など)に割り当て、その隙間を詰める最適生産スケジュールを作成すれば、生産時間は効率的に短縮できる。
最適生産順序の組合せは、10品目生産の倍は360万通り、15品目の場合は1兆3000万通り、と人力では不可能な結果になる。そこでスケジューラーと呼ばれる生産のスケジューリングに用いるコンピューターソフトが活用できるのだ。
「アッチェレランド」は小日程中心の食品工場用のスケジューラーだ。複雑な生産工程を短時間でスケジューリングし、季節変化や品目数、単一の生地を使用する多品目生産、冷生地やシートなど中間製品など、あらゆる工場の条件を反映できる。優れたヒューリスティックなアルゴリズムによって極めて短時間に演算できるだけでなく、ラインごとの仕様原材料の原価や使用量、金額も算出できる。
実際にある工場に導入し、同ソフトにより最適配置を行ったところ、手待ち時間が解消され、同一生産条件で3時間25分も短縮する事が出来た。この3時間半こそ見えないアイドリング時間であり、生産性を低下させる最大の原因だ。これを解消することにより、労務費が削減され、生産性を向上できる。大型パンでこのような結果が出るのだから、多品種少量生産のロールラインや菓子パンラインでは1日に6〜7時間の見えない手待ち時間が生じているのは容易に想像できるし、実際その通りだろう。
このように製パン工場では、各工程の組合せが余りに複雑だったため、手待ち時間に対し有効な解決策が無かった。しかし、文明の利器であるスケジューラーで最適順序を算出できれば、例えば従業員100人の工場で、1人あたり1時間の効率アップをすると(時給1,000円で計算)、1日あたり10万円、300日稼動で3000万円の削減になる。このような合理的なシステムを導入し、食品産業は生産性を向上し、国際競争力のある産業に今すぐ変革しなくてはならない。
【講師】弘中泰雅氏:鹿児島大学大学院終了後、製パン会社勤務をへて、1987年船井電機で家庭用製パン器開発に携わる。その後、2000年にテクノバ鰍設立し、代表取締役に就任。1988年には、九州大学農学博士号も取得。
|
|
|
ベーカーズタイムス 平成15年4月10日 木曜日 |
「生産性の向上」をテーマに
日本パン技術研究所が4月講演会
(社)日本パン技術研究所(井上好文所長)・研究調査部は4月14日(月)、以下の内容で4月講演会を開催する。
▽内容「生産性の向上」=パン産業の低生産性の原因分析から、新規開発した生産性向上システムの効果と事例など
▽講師=テクノバ轄O中泰雅氏(略歴=76年鹿児島大学大学院卒業、製パン会社に入社/87年船井電機入社、家庭用製パン器開発/88年農学博士(九州大学)/00年テクノバ叶ン立)
▽日時=4月14日(月)14時〜16時
▽会場=パン科学会館5F(東京都江戸川区西葛西6丁目19・6
《問合先・申込》03(3689)7571 |
|
|
ブランスリー 5月号 平成15年5月 |
モバックショー モバックセミナーレポート
パン工場の生産性はなぜ低い?
IT化で生産性は飛躍的に向上
テクノバ 弘中泰雅社長
製パン工場の労働生産性が低いのは、日配商品で日々の生産量の変化が大きく、しかも受注生産で中長期の生産計画が立てづらいからだ。しかも多品種少量生産で、多数便の出荷配送を行っているために効率的な生産順序で生産できないときている。従業員の手待ち時間の増加をもたらす。
例えば1ラインで10品目生産するとしよう。その生産順序の組合せは360万通り以上にもなり、もし20品目以上生産すればまさに天文学的数字になってします。人の能力でその効率的な生産順序を検証することは不可能だ。
このような製パン工場の実態から脱却し、生産性を向上させるために、Acceleranndo(アッチェレランド)は、日々の注文数に基づく生産数量から合理的な生産パターンを提案する。ラインごとの特性や、工程ごとの人数などのリソースを考慮に入れた判断も出来る。実際に生産する前に生産パターンをシミュレートすることも出来るし、固定的な順序で工程ごとの所要時間や終了時間も算出できる。この他、原材料の所要量も算出するので、実使用(出庫量)との比較により原材料の無駄の監視や、適宜材料単価を更新していけば、製造原価の算出も
リアルタイムで出来る。
すなわちIT技術を製パン工場に取り込み、生産性を向上させることを目的としたシステムだ。 |
|
|
パンニュース 2003年(平成15年)3月25日(火曜日) |
4月講演会を開催
日本パン技研
(社)日本パン技術研究所は、業界関係者向け講演会を開催することを決め、参加者を募集している。
【日時】4月14日(月)午後2〜4時
【場所】パン科学会館(東京都江戸川区西葛西6-19-6
【講師】テクノバ・弘中泰雅氏
【内容】テーマ「生産性の向上」
▽パン産業の現状と環境変化
▽電機業界の生産性向上の方法論
▽パン産業の低生産性の原因分析
▽スケジューリングとは
▽新規開発した生産性向上システムの機能
▽効果と事例
▽死して務の説明とまとめ |
|
|
パンニュース 2003年(平成15年)3月25日(火曜日) |
2003モバックセミナー セミナー・講演会
「アッチェレランド」食品生産管理ソフト
テクノバ社長 弘中泰雅氏
この25年間に産業別生産性がどれだけ変わったかというと、日本の機械産業、自動車や電機は3倍とか10倍とかで生産しているが、食品関連では1.29倍しか伸びていない。要するに1%にも満たない年成長だということである。パンを含む食品業界が、このままで本当に国際競争に勝っていけるか、一番懸念しているところである。
例えばアメリカは非常に生産性を問題視しており、生産性が向上していることによって経済が拡大しているという事実がある。
生産のスケジューリングに用いるソフトをスケジューラーと呼ぶ。パン製造に用いるスケジューラーは単一の生地から多くの製品をつくる、しかも受注から生産指令までの時間が短く、短時間で生産指令を出さなければならない。「アッチェレッランド」の生産指示はウインドウから行う手入力のほか、各工場にあった入力方法に調整出来る。
また、既存のコンピューターのシステムの一部だけ変える事も出来るし、材料管理、使用量、商品の原価まで出るようになっている。さらにシミュレーション機能もあり、機材の能力を買えて見た場合のケースの結果も引き出してみる事が出来る。実際に、新規投資や機械の入れ替える前に検討できるというのは大きなメリットといえよう。 |
|
|
ブランスリー 2月号 平成15年2月 モバックショウ特集ー出展社紹介 |
コスト(人件費)削減こそパン産業生き残り唯一の道
低成長下で利益を確保するためには経費を削減するしかありません。製パン業の生産原価に占める人件費の割合は全ての産業の中で最も高いのが現実です。
アッチェレランド(生産性向上システム)
パン工場の生産性が低いのは短納期で、製造条件の異なる多品種少量生産をせざるを得ないからです。現実的には人間の力で合理的な小日程を作成することは不可能です。従って成り行きのスケジュールや経験と勘にたよるスケジュールが幅を利かせていました。
問題は、長いて手待ち時間です。アッチェレランドはテクノバ独自のアルゴリズムで膨大な計算を短時間で処理し、ラインに最も適した生産計画を提示します。これに従って生産を行えば手待ち時間が解消され、稼動時間が大幅に削減されます。人件費だけでなく、光熱費なども削減されます。
ロンド(シフトスケジューラー
ベーカリーチェーンの採算性が目立って低下しています。店のスタッフの人件費が重くのしかかっています。変動する生産量や販売量の中で、アルバイト、パートの都合を考慮しながら、勤務シフトのスケジューリングをする事は大変な事です。これが店長により店の収益性が変わる最大の原因です。ロンドは個人の勤務の希望を入れると、職能や先月の勤務実績と日々の必要人員をもとに、各スタッフを公平に配置するシフトスケジューラーです。 |
|
|
パンニュース 2003年(平成15年)3月5日(水曜日) |
日本穀物科学研究会第131回例会
「食品工場の生産性と経営工学的取り組み」 弘中泰雅氏
食品製造業の過去25年間の生産性の向上は1.29倍で、年率1%にも満たない。この間化学工業は約11倍、電機は12倍、自動車は3.4倍になっている。失われた10年といわれるが、食品産業は25年間生産性の向上に関しては停滞してきた。
2006年を頂点に日本の総人口は減少に転ずる。今まで人口増加と食生活の欧米化により、パン生産量は増加してきたが、この16ヶ月は連続してパン生産量が前年割れとなっている。
パン製造業はいわゆる多品種少量生産で、短納期の生産量の確定もなしで生産を行ってきた。今まで生産量の拡大により、機械化の促進でパン製造業は発展してきたが、今後は消費停滞あるいは減少が確実視され、余剰生産力が存続する現実の中で、個々の企業の生き残る道は生産コストの削減しかない。売り上げの伸びが期待できない以上、生産性を向上させ経費を削減し利益を確保すべきである。
生産計画へのコンピューターの導入が早かった化学工業、製鉄業そしてかんばん方式、アンドン方式、アミーバー方式、屋台方式など多くの生産システムで生産性を上げた電機産業や自動車産業に比較し、経営工学的取り組みの少なかった食品工業は、まだ生産性向上の余地がある。例えば食パンラインで30%、菓子パンに至っては45%の手待ち時間がある。ゆえに20〜30%の生産性向上は、生産計画の作り方一つで可能になる。
食品の多くは典型的なフローショップ型生産で時間に縛られるため、生産計画が難しく、生産計画作成にコンピューターの導入を阻んできた。そこで、このフローショップ型の生産に使える生産計画ソフト(スケジュラーラー)「アッチェレランド」の開発に取り組みその有効性を検証したのでここに紹介したい。ここではパンを中心に説明するが、そのソフトは水産練り製品、製麺などのフローショップで作られている多くの食品に利用可能である。
食品生産ではガントチャート上に表される工程は階段状になる。各アイテムは生産数、工程条件の違いにより、異形の階段になる。異形の階段は並べ方、すなわち生産の順番で順列の幅(生産所要時間)が異なってくる。この差が前述の手待ち時間の差になって現れる。
1ラインで40種類の製品を作れば約3×10の18乗の並べ方があり、現在のパソコンで全て計算すると200年くらいかかることになる。当然人間の能力で完全最適なスケジュールを作る事は不可能で、仕方なく経験や勘に頼る非能率な生産計画のもと生産が行われてきた。
我々はヒューリスティックなアルゴリズムにより5分程度の時間で近似的最適解まで到達しうる。実用的なスケジュラー「アッチェレランド」によって食品工場の生産性向上に寄与したい。既に導入した工場では着々と成果を上げている。国際価格の6倍もする穀物、中国などの安い労働力など食品業界を取り巻く環境は厳しい。25年間の停滞を取り戻すためにも経営工学的手法を取り入れて生産性の向上に取り組まなければならない。 |
|
|
パンニュース 2003年(平成15年)2月15日(土曜日) |
パン工場を儲かる体質へ
生産性を上げるアッチェレランド
テクノバは、製パン工場の生産性向上ソフト『アッチェレランド』をモバックショウで紹介する。既に各地の中堅製パン業者からも引き合いがあり、同ソフトを導入した大阪の業務用大手メーカーでは、従来のコストと比較して30%の削減に成功している。
パン工場は、数ある製造業の中でも「最も生産性の低い工場である」と言われることもあるが、その理由は多品種少量生産に起因しており、製品間の待ち時間が多いことで、トータルな生産性が低下してしまう。この時間は、全生産時間に対して食パンで2〜3割、菓子パンなどの多品種生産のアイテムでは3〜5割に及ぶという。にわかには信じられないという人も多いだろうが、実際に所要時間か理論時間を差し引いてみるとわかるはずだ。
またこの時間は、いくら既定の生産順序で生産計画を立てたとしても、生産順序の組合せを効率のよいものに変更しなければ向上は難しい。1ラインで10の18乗の組合せが可能なパン工場において、人の能力だけでは合理的な生産計画を立案する事は不可能に近いものなのだ。
業務においてはさらに、納期やその他様々な制限要素が加わる。だからこそ、同社の食品工場用生産計画スケジュラー『アッチェレランド』の存在はパン工場にとっては朗報で、「今まで膨大な時間をかけていた計算が生産数量を入れるだけで、5〜10分程度の時間で終了する」という。
同ソフトは、最善の効率を求めてライン毎に毎日新たな計算を行えるのは当然のこと、特定の順序を入れ替えることが出来る”順序指定”、”過去の結果表示”、”材料原価”、”使用材料コスト”、”材料使用量表示”といった機能を備えている。また,」新製品の導入を考えた場合には、事前に生産シュミレーションを行い、設備変更の事前検討ができ、むだな設備投資や製造現場の混乱を防ぐことなどにも活用が可能だ。「既に導入した工場ではその成果が着実に上がっている」と確実に実績を作っている。
同社では「今後、国際的な競争はますます厳しくなり、新たな競争相手が違った形で形で現れてくることも考えられる。メーカーにとって利益の元は工場にあり、生産性を向上し生産コストを圧縮する利益体質に変えなければ、企業はさらに厳しい方向へ向かってしまう。だからこそ『アッチェレランド』のすばらしさを知ってもらいたい」という。
また同社ではベーカリー用のスタッフ配置ソフト『ロンド』も計画中。同ソフトは、リテイルベーカリーの経営を左右する労務費の削減につながるものだ。店長の人事管理によって、店が利益を上げるか、赤字になるか決まる場面もある中で「スタッフの配置をより合理的に行い、店にも従業員にも最適な勤務スケジュールを作成することが可能になる同ソフトを使用し、店の繁盛につなげてもらいたい」とかたる。
同社では、ブースでこれらのソフトのメリットを紹介をするとともに、モバックセミナーでもメリットを訴えていく。
|
|
|
ベーカーズタイムス 平成15年2月10日 月曜日 |
パンメーカーで初めてスケジューラーが稼動
食パン2ライン合計で人件費が8%台に
目標の数値化で社員の意識も向上
多くの電気、自動車等の製造工場で生産性を向上させる為に導入されているスケジューラーが、食品産業で初めて稼動し始めた。
稼動開始したのは業務用パンメーカー潟Iリエンタルベーカリー(本社=大阪市浪速区、原田幸博社長)の泉佐野工場で、導入したスケジューラーはテクノバ梶i大阪市浪速区、弘中泰雅社長)が開発した『アッチェレランド』という食品工場用生産スケジュール管理ソフトだ。
今回は原田社長に、アッチェレランドを導入した経緯と、稼動後の効果等の話を聞く事が出来た。・・・・・・・ (略)・・・・・。昨年4月の時点で9.6%だった食パン2ライン合計の人件費率が、今では7〜8%台まで下がっています。・・・・・(略)・・・・・・・・・ 各作業時間や人員はこれまでとまったく同じ能力なのに、組合せを変えることで終わる時間が早くなる。数十種類のパン製造工程を人が全て組み直す事は出来ませんが、パソコンでシミュレーションすれば、一番良いものと悪い物との対比ができます。今までは部分的に見て、これが一番良いと思ってやっていたことが、トータルではそうでないとはっきり数値で示されると、意識が変わり納得できるのです。・・・・・(略) ・・・・・・・
今、パン業界全体に元気がありません。これが一つの起爆剤となり、業界全体が向上していけばと思っています。 |
|
|
ブランスリー 9月号 平成14年9月 |
中国パン工場視察雑感
生産性はまだ低いが・・・・・
(本ホームページ Shows
& Reports参照) |
|
|
食品機械装置(ビジネスセンター社) 5月号 |
@生産性がいかに食品企業の経営を左右するか
A食品製造業の生産性の現状
Bスケジューリング
C食品工場の生産管理
D食品工場用のスケジューラー
E実際の製造記録とスケジューラーによる生産スケジュール |
|
|
製菓製パン 2002.4 |
テクノバ(株)が生産性向上ソフト アッチェレランドを発表
多品種少量の複雑な生産に対して有効性を発揮
テクノバ(株)(大阪市・弘中泰雅代表取締役)が製パン工場の生産性向上ソフトウエア(スケジューラー)であるアッチェレランドを発表した。
これは、多品種少量の複雑な生産に対して有効性があり、パン以外にも水産練り製品、麺、菓子などの食品工業、またそれ以外のゴム、プラスチックなどの成形品の製造や調剤薬局の効率化、シフト管理のスケジューラーなど、その用途は広く期待されている。
今回は、(株)オリエンタルベーカリーにも導入され、その実用性が証明されたかたちとなった。パン工場の中で最も生産性が高い食パンラインで、窯や分割機の正味の稼働率は70%といわれ、より多品種を生産する菓子パンなどのラインではそれが50%程度になるという。その大きな原因は、作業者にとっての手待ち時間(アイドリングタイム)にある。そのため、生産性を向上させるには、この手待ち時間を生じさせない作業の組み合せ(生産のスケジューリング)が必要になる。
しかし、10種類のパンの生産順序組み合せは360万通り、15種類だと1兆3000万とおり、人間の力では不可能に近い。そこでコンピューターソフトを使用して、合理的なスケジューリングを行なう必要が出てくる。実際に導入したオリエンタルベーカリーの原田社長は、既に効果は上がっており,最終的には30%程度の生産性向上が期待できると語っている。 |
|
|
製菓製パン 2002.3 |
パン工場の生産性を改善するソフト開発
【大阪】ソフト開発会社のテクノバ(大阪市浪速区、弘中泰雅社長)では、パン工場の生産性を改善するソフト「アッチェレランド」を開発した。
パン工場と家電メーカーの両方に勤務した経験のある弘中社長が食品業界の生産性を向上させるため、電気製品の効率的な製造システムを応用したソフトを開発。準備から二年以上かけて特許を出願した。
パン製造では、@多品種少量生産A毎日注文が違うB発酵など時間短縮ができない工程が多いなど、さまざまの問題があり、生産ラインでの作業スケジュールが合理的に進まないことが多かった。
また、作業員のアキ時間を生じさせないように作業スケジュールを調整することも工程が複雑なため難しく、職人のカンに頼る部分が多かった。
開発したソフトを用いると、独自の計算方法によって、製造するパンの種類や数を入力するだけで約一分、種類が多い場合でも5分程度で合理的な作業スケジュールを算出する。
実験によると、このソフトのスケジュールに従うと、これまでより作業時間が約三時間短縮されたという。パンの製造条件や原材料のデータベースが作れるほか、新製品投入などのシミュレーションも可能だ。
パン業界のほか食品業界全般はもとより、多品種少量生産にたずさわる、さまざまな分野に応用できる可能性を持つ。
このソフトを導入したオリエンタルベーカリー(大阪市浪速区)では、約二百種類のパンを製造しているが、従来の職人による手書きのスケジュール表よりも約二時間の工程効率化ができるとみており、年間人件費三割減をめざす。
同社の原田社長は「いいものを作ろう、からいいものを早く安く作ろうへと社員の意識が変わった」と語っている。 |
|
|
パンニュース 2002年(平成14年)1月15日(火曜日) |
テクノバ
生産性向上ソフトを発表
「アッチェレランド」 |
|
|
ブランスリー新聞 2001年12月20日 |
パン工場の生産性を向上
パソコンソフト本格始動 |
|
|
日経産業新聞 2001年12月17日(月) |
パン製造ライン管理ソフト
待ち時間を圧縮 テクノバ
食品メーカー用生産管理システム開発のテクノバ(大阪市、弘中泰雅社長)は
製パン工場向けの最適な生産スケジュール管理ソフトを開発した。日配品で多品種少量生産を強いられるパン製造は工場内のアイドリングタイム(待ち時間)が長く、一般的に生産性が低い。同システムの使用で生産性を2-3割引き上げることが可能である。中小製パンメーカー向けに売り込む。
ソフトの名称は「アッチェレランドベーカリー」で、第1弾として中堅製パンメーカーのオリエンタルベーカリー(大阪市、原田幸博社長)に納入した。当日の朝に生産品目・量が確定するのに合わせて、生産品目と生産数を入力すると、数分で30程度のラインごとの生産スケジュールを提案する。オペレーターはこの提案の中から、工場の実情に合わせて選択できる。
従来、熟練社員の経験やノウハウで当日の生産工程を決めているケースが多いが、同システムでスケジュール化すれば、1日で3時間程度の時間短縮が可能になるという。オプションとして、原材料管理、コスト管理などの機能も付けた。ソフトの価格は当該工場の労務費の5%程度を目安とする。
製パン業は発酵、ホイロ、焼成など生産工程が多く、特に製品種類の多い菓子パンを主力とする工場の稼働率は5割程度という。テクノバは製パンメーカーへの販売と平行して、かまぼこなどの水産加工メーカーや医薬品・健康食品の製造会社にも販路を広げる。 |
|
|
産経新聞 (西日本版)2001年12月13日(木) |
パン工場の悩み改善ソフト開発
テクノバ 大阪で本格的実用
ソフト開発会社、テクノバ(大阪市浪速区、弘中泰雅社長)は、パン工場の生産性を改善するソフト「アッチェレランド」を開発した。効率的な作業順序などを短時間で算出する工場専用ソフトで、今月からパン製造会社、オリエンタルベーカリー(大阪市浪速区、原田幸博社長)の工場で本格的な実用が始まった。
パン会社と家電メーカーの双方に勤務した経験をもつ弘中社長が、食品業界の生産性を向上させるため、電気製品の効率的な製造システムを応用したソフトを開発。準備から二年以上かけて特許を出願した。
パン製造には、多品種少量生産▽毎日注文が違う▽発酵など時間短縮できない工程が多いーなどの課題があり、生産ラインでの作業スケジュールはむだが多くなりがちだった。また、作業員の待ち時間を生じさせないよう作業スケジュールを調整するのも工程が多く複雑で、職人のカンに頼る部分が大きかった。
開発したソフトは独自の計算方式により、製造するパンの種類や数などを入力するだけで通常で約1分、種類が多い場合でも約5分で合理的な作業スケジュール
を効率の良い順に表示する。実験を重ねた結果、合理的に計画されたこのソフトのスケジュールを用いると、これまでよりも作業時間が約3時間短縮されたという。
個々のパンの製造条件や原材料などのデータベースが作れるほか、新製品投入などのシミュレーションも可能。同社では食品産業全般での応用に加え、薬品製造やネジなどの多品種少量の製品を扱う中小製造業者の利用も視野に入れており、さまざまな分野に合った改善ソフトを提案していく。
約200種のパンを製造するオリエンタルベーカリーでは、ソフト導入で従来の職人による手書きスケジュール表より約2時間の工程効率化が出来るとみており、年間人件費の約3割削減をめざす。原田社長は「ソフトを導入して、職人の意識が『いいものを作ればいい』から『いいものを早く安く作ろう』と変わってきた。生産性を上げて積極的な新製品開発に力を注げるようにしたい」と話している。 |
|
|
みなと新聞 2001年12月11日(火) |
コンピューターソフト「アッチェレランド」 テクノバ
効率的加工へ生産工程作成
【大阪】テクノバ梶i弘中泰雅社長)が開発した「アッチェレランド(Accelerando)」は食品加工の効率的な生産スケジュールを作成するコンピューターソフト。工場内の各ライン工程の空き時間を合理的に削減し、作業者の負担を増やすことなく生産性を向上させる優れものだ。「アッチェレランド」は、食品生産の膨大な生産順序の組合せの中から、注文量や各工場の製造条件、原材料、季節による生産条件の変化などの実情に合った合理的な生産スケジュールを独自の計算方法で導き出し、分かりやすい工程表として出力する。
食品15種類の生産順序の組み合わせは1兆3000万通りと膨大な数になるが、アッチェレランドはそれぞれの工場にあったパラメーターを設定し、合理的な計算を行なうため、わずか5分で上位30工程の生産順序を提示できる。そのため、毎日の注文数の変動や飛び込み注文にも簡単に対応が可能だ。
また、作業者が工程表の指示に従って作業を行なえるため、無駄な時間がさらに短縮される。セキュリティーの面では、操作範囲を権限により制限するなど、機密性や安全性を考慮しているため安心。原材料管理、コスト管理、生産のシミュレーションの機能も付いており、整備の見直し、新製品投入時の生産ラインに対する影響を事前に検討できる。今月から「アッチェレランド」を導入したパン製造メーカーの潟Iリエンタルベーカリー(原田幸博社長)は、同ソフト導入で
生産効率が20〜40%向上することを期待できるほか、効率的な生産効果から「人件費の3割削減を目指している」(原田社長)といい、食品業界からさらに注目を集めそうだ。 |
|
|
ベーカーズタイムス 平成13年12月10日 月曜日 |
テクノバ 食品工場生産性向上ソフト
「アッチェレランド」が完成
オリエンタルベーカリーが導入 |
中小製パン工場における生産性向上の限界を探る
アッチェレランド導入で人件費30%削減目指す
潟Iリエンタルベーカリー代表取締役社長 原田幸博氏
当社がこのソフトを導入する目的は二つあります。一つは工場の生産性を上げる事ですが、もう一つは当社のような中小の製パン工場が生産性をアップできる限界はどこまでかを知りたいということです。そして、当社がこれから戦える分野はどこなのか、戦える品目はどういうものなのかを探っていきたいと思っています。今まで全くわからなかったのですが、このソフトを導入することで分かるだろうと考えています。
これからは中国で生産された低価格のパンも日本に入って来るでしょうし、このままでは戦えないでしょう。でも、本当に戦えないのか、それも知りたいと思っています。
当社でも、生産現場はその日の仕事が何時に終わるのかわかりませんでした。パートをいれるのでも、どのくらい必要なのか正確に分かっていないので、計画しなくなり考えなくなる。だから全体として非常に効率が悪くなるという悪循環です。また、イーストを使うので発酵を伴うし、生産量も変わるので時間が読めない。良いものを作る為には生産性というものが馴染まないと皆が思っています。時間を確定させると悪いものが上がる。もし、何か失敗が起こると、今まで以上に丁寧に時間をかけてやるようになるので、更に長時間労働になる。品質重視という面では正しいのでしょうが、これでは計画が出来ないので、若い人が入ってこないし、後継者も育たない。工場で働いている人達は人に使われているという意識になり、自分で考えなくなり意欲がなくなる。当然全体のレベルは次第に低下していきます。
このままではいけないということで、当社でも曜日毎に分けた7種類のスケジュール表を前日に作るようにしました。手作業で作ったスケジュール表なのですが、そのスケジュール通りできているときは全く問題がありませんでした。しかし一ヵ所でも遅れがでると、全部が用心して遅れがどんどん長くなって、最終的には一ヵ所の遅れの何倍もの遅れになってしまします。何故だか分かりませんが、手作業でのスケジュールではもう一つ信頼性に欠けるのか、パソコンでの出力に変更したら、一ヵ所の遅れがそのまま後にズレるだけで済むようになりました。
ただ、この工程作りに一日費やしてしまいます。これでは考える時間がとれません。しかしこのソフトなら最適なスケジュールをわずか1分で提示してくれます。これで、他の色々なことを考える時間がとれます。計画生産が出来るようになり、やっている人が主体性を持って仕事に取り組めます。そうすれば従業員の意識が変わり、社内にカルチャーが醸成されていくと思います。
当社ではスケジュールを手作業で作った時に5%、パソコンでやった時に10%人件費が下がりました。いかに隙間が多かったのかと感じています。私はこのソフトを導入することで、人件費を30%下げたいと思っていますし、多分それは可能だろうと思っています。 |
|
|
食品産業新聞 2001年12月10日(月) |
パン生産ソフト オリエンタルべーカリーに導入 テクノバ |
|
|
米麦日報 2001年(平成13年)12月5日 |
生産性向上ソフト「アッチェレランド」1号機導入
製造工程短縮、人件費3割減=オリエンタルベーカリー |
|
|
製菓時報 2001年12月3日(月) |
テクノバ パン生産管理ソフトを開発
菓子などへの応用も可能 |
|
|
ホイートクラブ 2001年10月号 |
店舗紹介 クックハウス阪急三番街店
(略)
「お客様の要望に応えられるような商品はやはり本社工場でないと作れません。そして、手間をかけた商品は確実に売れる商品となります。ですから私はいつも社員に、よそより手間をかけた商品を作るようにといいつづけています」
「しかし、商品に手をかけるだけでは肝心の経営が成り立たなくなります。」それで今年から、製パン工場の生産性向上ソフトを開発し、加工技術の開発とコンサルティングをされているテクノバ鰍フ弘中泰雅さんに色々な面でアドバイス頂いています。まだ、ソフトの稼動には至っていませんが、こういう取り組みをすることによって、社内的な雰囲気が随分良くなってきたと感じています。」
(略) |
|
|
ベーカーズタイムス 平成13年8月10日 金曜日 |
製パン業界とパラダイム・シフト
パラダイム(Paradigm)と言う言葉をご存知だろうか、研究社の英和辞書(New Collegiate)(1992)によれば、1《文法》(品詞)の語形変化表、2 例、模範、典型 と書いてある。三省堂の新明解国語辞典には、範例(語形変化)のギリシャ語に由来(略)することなど、比較的詳しく書いてある、その中で「その分野における思考の枠組や・学問(芸術)の方法論、共通の基準の意にも用いられる」とある。
以前私が籍をおいた電機業界のAV関連記録メディアの変遷をとってみるとSPレコード、LPレコード、カッセットテープ、VTRを経て、CD(LD)、DVDなどの光ディスクと移り変わり現在はCDRW、DVDRW?、 続いて高密度HD、次世代DVDなど次の主役を模索している。
10年前にはアナログディスクとディジタルディスクの音質について口角泡を飛ばして議論したものだが今ではLPレコードの影もすっかりなくなり、レコード店の言葉も死語になりつつある。
即ちエジソンの蓄音機に始まる録音録画の歴史の当にパラダイム・シフトの連続である、当初エジソンは蓄音機にたいした商業的価値を認めなかった。 エジソンすら自ら発明した新しいパラダイムを認識することが、出来なかったのである。
しかしながらエジソン以降次々と上述のごとく新しいパラダイムが作り出されていった。パラダイムは規範すなわち一種のルールであるから、ただ蓄音機からDVDに製品が変わっていったということだけではない、それぞれの物には、たとえばRIAAとかドルビーのような規格が背景に有る、有名なβ方式、VHS方式の戦い、現在ではDVD-R/RWかDVD-RAMかの勢力争いのまっただ中に有る。 ルールは法律で規定されていようと、デファクトスタンダード(事実上の規格)であろうとルールはルールである。
パラダイムシフトしフェーズがある、新しいルールが発見されるフェーズA, 新しい産業が生まれるフェーズB, 問題解決に行き詰まるフェーズCである。 全ての製品はこのフェーズを通過する。
パラダイムは一種のルールであるから、分かりやすい例を挙げよう、皆さんが子供さんを育てられていれば、一度や二度いやもっと経験された例である。 何でも良いが、例えば小さな男の子が今まで興味の無かった野球の中継をTVで突然見るようになる、そして「お父さん野球わかるよ」という。 この子は野球のルールを理解した即ち野球というパラダイムを発見したことになる。 今まで小さなバールを棒でひっぱたいて大の大人が追いかけていくに過ぎなかった番組が彼にとって野球になったのである。
パラダイムは発見され、発展し、新しいパラダイムが発見され追い抜かれパラダイムシフトが起きる。 金融の護衛船団方式というパラダイムが壊され、金融の自由化、自己資本比率の制限など新しいパラダイムの中で金融経済は喘いでいる。 価格破壊も為替の変動を積極的に利用し、材料を安く買い、海外で安く品質の良い商品を調達し、低コスト販売をするという新しいパラダイムを発見発展させたことによって起きてきた.。
日本農業の生産性は驚くほど低いその結果日本の野菜は高い、そこで海外で日本人の好む野菜を安く生産すればどうなるか、新しいパラダイムである。 いくら農業白書で日本農業の自給率向上を訴えても食糧自給率は低下するばかりである。 最近の速報では米の消費がやや増加してきているようである、何とその理由が牛丼などの廉価販売によると分析されている。 新しいパラダイムは米の消費をも回復させる可能性を秘めている。
翻って,パン業界において新しいパラダイムはどうであったか、無論大手の伸長、流行の商品の変化,他業種の参入など多くの変化がパン業界をゆるがした。 しかし技術の分野に限ってみれば、この間に製パン技術に関する変化はどれほどあったであろうか。 数千年の歴史があり、人の口にするパンが先端技術の電機機器に比べて変化が難しいことは致し方ない事としても、本質的な変化はやはり少ないといわねばならない。
いまパン業界に必要なのは新しいパラダイムである、消費者の求めている商品、コスト競争力を生み出すシステムにパラダイムシフトしなければならない。
最近西陣織りがセーフガードの発令を要求した、廉価の中国製の輸入絹織物に困った末の策であろう。 西陣織りといえば高級織物の代表である、ところがこのセーフガードの発令は、西陣織ブランドの競争相手はエルメスやフェラガモブランドではなくて、中国製品で有ることを自ら、公言したことに他ならないことをどれだけの人が気づいているのであろうか。
パン業界も徐徐に直接間接に、グロバリゼーションの波に洗われるのは間違い無い。新しいパラダイムを発見し、国際化に耐えうる新しいパラダイムにシフトしなければならない。 昨年の食品事故の多発は幸いにも新しい食品衛生管理のパラダイムを確立させようとしている。 新しいパラダイムを発見することは難しい、皆でパン業界のパラダイム・シフトを考えて見ようではないか。
|
|
|
ベーカーズダイジェスト 7月号 |
製パン業界とパラダイムシフト |
|
|
ベーカーズタイムス 平成13年4月10日 火曜日 |
パン産業の為の生産管理システムを提案(モバック2001のセミナーから)
@日本経済の現状
先般の日経新聞で「経済成長率より生産性の議論を」というコラムがあり、日本経済の景気が悪いのは、生産性が低いからだと書かれています。日本の生産性は米国の三分の二で、生産性を上げなければ経済の回復はないということです。そしてこの低い生産性の中で最も低い産業が製パン業なのです。
A経済構造の変化
今回の不況下でその1年間の株式時価総額ランキング企業をみると、上位企業が大幅に入れ替わっています。かつての基幹産業であった鉄鋼、重工業はトップ20から消え、金融業を除くと、いわゆるIT産業とトヨタ自動車、ソニー、本田技研工業などの生産性の高いメーカーばかりです。いかに昨今の日本経済の産業構造が激変しているかということと、メーカーにとって生産性がいかに大切であるかということが分かります。
Bパン業界の実情
パン企業で生産性の話をしますと、多くの企業で出てくるのが設備増強と作業者個人の技量アップという言葉です。コストを考えないで、ゆとりのある設備で生産すれば、労働者・時間あたりの生産性は向上しますが、工程の手待ち時間は増加し、設備の稼働率はますます低下する可能性があります。一人一人の技量が極端に低ければ問題ですが、それよりもマンパワーを効率よく引き出すことが真の効率の向上につながるのです。
C隙間だらけの煩雑な作業スケジュール
それではなぜパン工場は生産性が低いのでしょう。現実の工場に日報に現れた稼働時間と、算出した稼働時間の差異はパン工場の待ち時間に対する認識がいかに低いかを物語っています。手待ち時間こそ製パン産業の生産効率の低さの現況なのです。そしてこの手待ち時間は製パンの全ての工程に存在します。
Dパン産業にあった生産性向上システム
世界に誇る日本の電機業界の生産性の向上の源泉は、特別な設備ではなく、普通の女子社員が並んで人海戦術で製品を作っていることにあります。但しそこにはその産業にあった研ぎ澄まされたシステムがあるのです。パン産業の生産性が低いのは、未だにパン産業にあった生産システムが構築されていないことにあるのではないでしょうか。
それぞれの工場にあった最短のスケジュールを選び、それぞれの工程ごとの計画時間を設定し、それに従って作業を進めていけば、作業者に過度の負担をかけることなく自動的に作業時間の短縮ができます。
Eテクノバアッチェレランドの概略
複雑であるが故に、経験と勘に頼らざるをえなかったパンの生産にIT技術を導入して合理的なスケジュールを作成し、生産性の向上を図る生産管理ソフトがテクノバ・アッチェレランドです。
このソフトは翌日の生産予定数を入力すると、各工場のデーターベースに基づいて、スケジュールエンジンが対話的に最適な生産計画を作り、工場あるいはラインを見渡すタイムスケジュールと各ラインの工程別スケジュールを作成し、これにしたがって作業者は作業を行なっていくわけです。この場合当然各工場はそれぞれ固有の制約条件を持っているので、これらは当然データーベースの中に組み込んでおきます。
導入に要する時間は、工場の規模、商品構成により異なりますが、現状分析の基本検討、工場に応じたカスタマイズのシステム構築、試験運転を含む導入運用、評価を含む本稼動まで、着手から完成まで各工場の実態調査、データーの整理等を含めて、半年から1年程度の期間を要します。 |
|
|
パンニュース 2001年(平成13年)3月25日(日曜日) |
製パン工場の生産性向上
近い将来、日本の総人口は減少をはじめ、国内の製パン市場は確実に縮小、さらには若年齢の減少は労働人口の減少といえ、今後の雇用条件は厳しくなっていくと考えられる。このような背景の仲で、製パン工場は今のような低い生産性のままでいたとすれば、今後発展の可能性は非常に難しいと考えられる。
このような状況をどうすれば打破できるのか?というと「生産性」を今一度見直し、高めるということだ。例えば、製パン工場を見てみると効率のよいといわれている食パンラインでさえ、「待ち時間」すなわち隙間があり無駄が多い。この隙間を改善することが、生産性を大幅アップさせる要因でもあり、当社の「パン生産性向上ソフト・アッチェレランド(Accerelando)」開発のきっかけともなった。このアッチェレランドを使えば、無駄のない仕組みが構築され、生産性が高まるのだ。
これまで製パン業界は、為替の変動などにあまり影響なく恵まれた産業だ。しかし、今後は「無駄がなく高い生産性」を持った企業のみが生き残れるのが現状となってくるだろう。
ある経済誌で「オールド企業の逆襲」という特集を組んでいたが「オールド企業がいかにITを導入するかで笑いが止まらない状況にになる可能性は十分にある」と思っている。 |
|
|
ブランスリー 4月号 平成13年3月20日 |
製パンラインの生産性が向上
21世紀を勝ち残るためには、生産性向上が絶対条件で、これからの日本は、人口が減り、大きな売上増は見込めないし、労働力を確保するのも大変になる。 経済のボーダーレス化により、製パン産業も国際競争にさらされる可能性が高い。10年前に土地バブルが崩壊した時に、株価が4割さがったが、株価の順位には大きな変動はなかった。この1年間の株価の下落にともなっては、株価の順位には大きな変動が見られる。現在は、経済活動に対する価値観が大きく変わっている変革期なのだ。
アメリカでは、IT革命により、IT関連産業の賃金は40%上がったと言われている。しかし、オールドエコノミーといわれる業種では、5%下がったといわれる。オールドエコノミーはいまこそIT技術を積極的に取り入れ、生産性を向上させなければならない。 |
|
|
ベーカーズダイジェスト 3月号 平成13年3月10日 |
パンの生産性向上ソフトを開発
当社が開発した生産性向上ソフト「アッチェレランド」は、製パン工場のラインの生産性を向上させるためのコンピューターソフトだ。製パンラインは、多くの種類のパンを生産するが、品目ごとの流れの列どうしの間隔を可能な限り縮めた状態でラインを稼動させようというもの。列車に例えて考えると、できるだけ過密ダイヤで列車を走らせようという趣旨だ。列車がどうしがぶつからないのは、ダイヤがあるためだ。「アッチェレランド」は、ひとつの品目の流れの列を、1本の列車にとらえ、製パンラインの効率的なダイヤを作る。
ただ、鉄道と違って、製パンラインの場合は、各品目の列(列車)が、工程ご
とに進む速度が違う。列車に例えれば、ある区間は急行で、ある区間は快速、ある区間では鈍行になるといった具合だ。このことが製パンラインの効率的なスケジューリングを困難にしている。アッチェレランドは、独自のアルゴリズムにより、各品目の列をどのように組み合わせて走らせたら、最も短時間で済むかを計算して、分かりやすい工程表として出力する。 |
|
|
ベーカ―ズタイムス 平成13年2月10日 土曜日 |
新世紀初のモバックショウ 2月22日から大阪南港で開幕
セッション10 「製パン工場の生産性の工場について」
テクノバ椛纒\取締役・弘中泰雅氏<問合先>06(6630)7812
Fax06(6630)7813 |
|
|
産経新聞 経済欄 平成13年2月7日 水曜日 |
My Way 製パンにIT導入
食品製造業界は、人件費がコストを圧迫するという。ソフト開発会社、テクノバの弘中泰雅社長は、食品と機械の両業界で働いた経験から、食品業界に機械業界の効率や正確性を取り入れた生産性向上ソフト「アチェレランド・ベーカリー」の開発に取り組む。
「生地を作ったりオーブンに入れたりするタイミングは、職人のカン頼りで時間ロスが大きい。コンピューターで効率のよい作業ダイヤを作ろうというわけです」 製パン業は工程が複雑なため、これまでIT導入がほとんど進んでいない分野。十種類の製品を焼き上げるためのスケジュールの組合せは三百六十万通りにもなる。
このソフトは各工程間の待ち時間などを減らした最も合理的なスケジュールを選出。それに従えば作業時間を約二割も短縮できるという。
輸入規制の緩和などから、「食品製造業界もいずれ海外との競争を余儀なくされる」と弘中社長。危機感の薄い現状を憂慮し、トータルな経営システムの見直しも提案する。
弘中社長は「お客さまに負担を負わせないで経費削減するには、労働力の効率化しかない。ソフト導入で職人達の意識も変わるはず」と話す。製菓や他の食品分野への応用も検討、来月から在阪のパン会社で試験運用を始めるという。 |
|
|
ブランスリー 2月号 2000年(平成13年)1月20日 |
出展します! 製パン工場の生産性を20〜30%向上させる!
テクノバ 小間番号 1‐119
★テーマ 製パン工場の生産性を20〜40%向上させる生産管理ソフト、「アチェレランド」を使用して、製パン工場をより効果的に稼動させることを提案する。同ソフトをパソコン上で実際に動かして、具体的にどのような形で生産を管理するかを実現する。 (抜粋) |
|
|
ベーカ−ズタイムス 平成13年1月10日 水曜日 |
メーカーとしての存続かけ生産効率向上が急務
重要なのは「価値創造」の為の生産効率の向上だ。現状からして売価の上積みは不可能に近いし、いずれは異業種及び海外からより低価格の商品が入ってくる可能性がある。とすれば、今の内に各製パンメーカーは一層の生産性の向上を図り商品競争力をつけておく必要がある。但し、機械化設備による合理化だけでなく、システムとして生産性向上を図る事を考える時期に来ている。 昨年、弊紙でも紹介したテクノバ鰍フ弘中氏は、他の業種に比較して製パン業界の低すぎる生産性を憂い、コンピューターソフトを導入した生産性向上の為のシステムを構築中だが、同氏によれば、殆どの製パン工程でまだ1〜2割の生産性向上の可能性は高いという。
電子商取引もIT革命の一つだが、製パンメーカーとして取り組むべきもう一つの重要なIT革命はここにもあるのではないだろうか。 (抜粋) |
|
|
パンニュース 2000年(平成12年)12月25日 (月曜日) |
ホームページ開設 関西穀物科学研究会
関西穀物科学研究会は、このほどホームを開設した。内容は前回の例会の講演や懇親会の様子などの簡単な報告と次回の案内など。運用は運営委員の弘中泰雅氏。アドレスはhttp://www.technova.ne.jp/kansaikokumotu.htmでテクノバ鰍フホームページと併設。 |
|
|
ブランスリー 12月号 2000年(平成12年)11月20日 |
製パンラインをダイヤ化 生産性が20〜40%向上
パン生産管理ソフト開発のテクノバは製パンラインの生産効率を20〜40%向上させる生産管理ソフトの販売を始める。現在中堅製パンメーカーの工場の実情に合わせた生産管理ソフトを開発中で、来年2月にインテックス大阪で開かれるモバックショウで発表の予定だ。
同ソフトの名称はアッチェレランド(だんだん速くの意味)。ベーカリーの効率的な生産スケジュールを作成するコンピューターソフトで、ライン各工程の空き時間であるアイドルタイムを合理的に削減し、作業者の負担を増すことなく生産性を向上させる。
製パン工場は毎日品目ごとの注文数によってラインを稼動させるが、経験的に決められた、ほぼ単一の生産順序のため受注の変動に対応できていないのが現状という。最も生産効率がいいとされる食パンラインでも、ラインが稼動している時間の20%程度のアイドルタイム(待ち時間)があるという。
アッッチェレランドはパン生産の膨大な生産順序の組合せの中から、注文や工場の状況などの実情に合った効率的な生産スケジュールを、独自のアルゴリズムで導き出して、わかりやすい工程表として出力する。作業者が指示に従って作業を行うことで、最も効率的な生産ができる。ラインの無駄なアイドルタイムを削減することで、労働生産性が、20〜40%向上する可能性があるという。
テクノバによると、日本の製パン産業は他産業に比べて生産性が極めて低く今後国際競争にさらされた場合などを想定すると苦戦を強いられるのは必至だと言う。テクノバの弘中社長は「パンの生産ラインの運行は鉄道に例えて考えていただけるとご理解いただける。過密スケジュールで電車が走ってもぶつからないのは、ダイヤ化されているため。アッチェレランドは乗客数に合わせて、電車が常にほぼ満席の状態で隙間なく走っている状態と同様に製パンラインを稼動させる為のコンピューターソフトです」と話している。 |
|
|
パンニュース 2000年(平成12年)6月25日(日曜日) |
「テクノバ」業務開始
製パン業などの生産性の向上を目指したコンピューターソフトの開発販売会社テクノバ(弘中泰雅社長)が5月に大阪で設立、業務を開始した。同社の弘中社長は以前製パン会社で研究開発に携わり、その後船井電機で家庭用製パン器の開発を担当した。 関西穀物科学研究会の監事も勤めている。
今、パン業界では中堅・リテイルを含めて人件費など、難問が山積みしている。 同社では各企業別にその企業個々の問題点を取り上げて解決法を提案するという。 |
|
|
ベーカ−ズタイムス 平成12年3月10日 金曜日 |
低いパン業界の生産性 国際競争力欠如の懸念
これからの国際産業界の雌雄は生産コスト、生産性が決めると言っても過言ではない、こんな中で製パン企業の製造原価に対する直接労務費比率は食料品製造業平均11.1%に対して、26.2%全ての主要な産業の中で最も高いひとつである。
パンは従来非貿易財であったため、国際競争に晒されることはなかった。 金融ビッグバーンの例からも近い将来、大きな変化を受け入れざるを得ない状況がかならずくる。 パン業界が最優先で取り組まなければならない課題は「労働生産性の向上』である。 この問題は取り組みでかなり大幅な改善がかのうである。
パンの製造は日配商品の中では生産が複雑なものの代表であろう。 複雑な工程の組合せである商品を一本のラインで多数生産するため、工程毎の処理速度が異なる、これが製パン工場運営の難しさであるが、結果としてアイドリング時間をを生み出し、しかもその認識がない。 パン業界の生産性の低さの最大の要因がここにある。
各社の実情をとりいれたシステムソフトを導入することで、約20%の労働生産性の向上は可能である。 |
|
|
 |